How To Choose The Right Air Compressor?
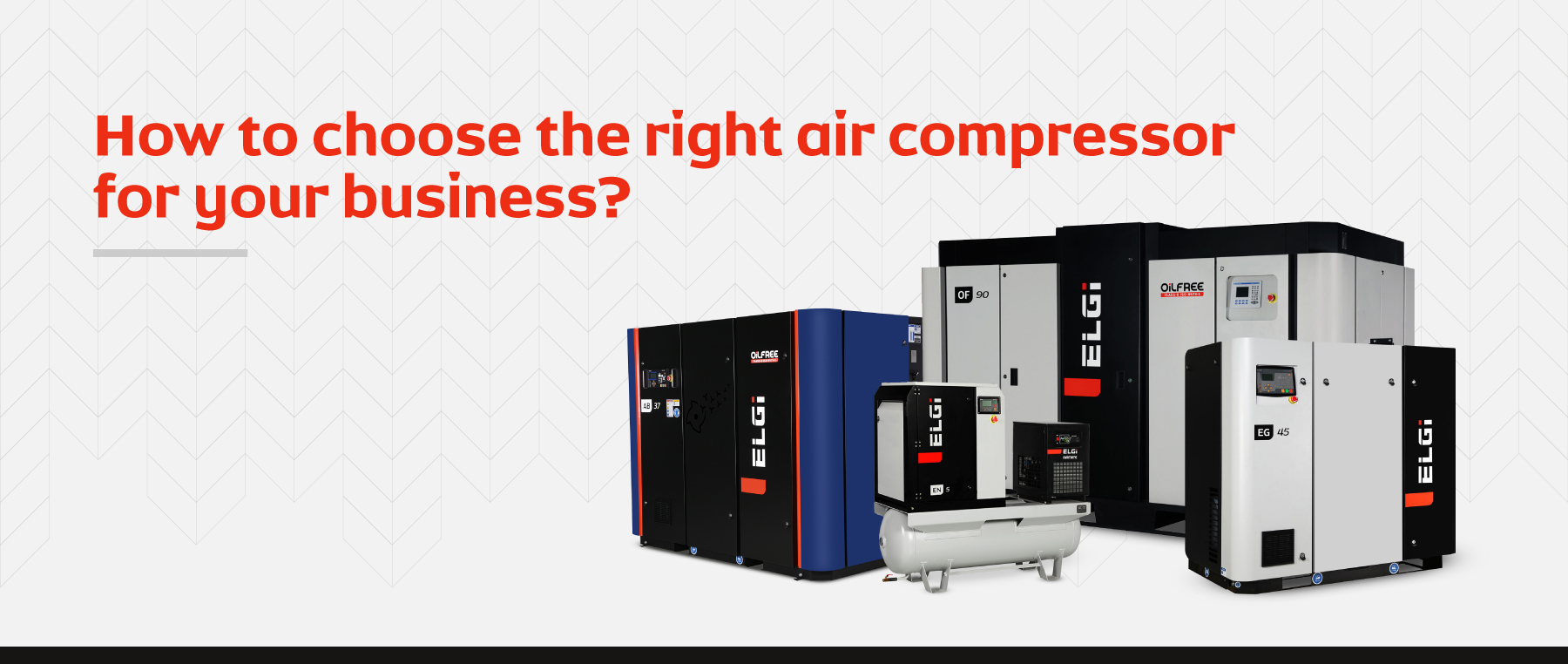
Compressed air is critical to many industries across many applications. Especially now, with the increase in automation across industries, the need for compressed air in the industrial sector is also rising – and this dependency will only grow going forward. With compressed air being essential to the operations of a business, choosing a suitable air compressor is fundamental to running smoothly and profitably.
At ELGi, we want to simplify the process of selecting the industry’s most widely used air compressors, reciprocating and screw compressors, for any given application. But remember, when in doubt, always reach out to our Compressed Air Experts!
Factors to Consider When Selecting an Air Compressor:
- Quality of Air
- Capacity of the Compressor Required
- Duty Cycle & Utilization
Quality of Air
Industrial compressors have oil as the medium that cools, lubricates, and seals gaps between the moving parts. As a result of this, compressed air is exposed to the oil and a part of it is carried over.
In specific applications, compressed air comes in direct contact with products such as food and pharmaceuticals. For zero-tolerance of oil contamination applications, 100% oil-free compressed air is recommended.
The quality of air based on the amount of this oil carried is represented by ISO 8573:2010. Class 3 allows for < 1 mg/m3 of oil carry over and a higher quality can be achieved through downstream filtration equipment.
Depending on your application requirement, the selection of the air compressor will vary.
Capacity of the Compressor Required
The capacity of an air compressor is a function of volumetric flow of air and the pressure to which it is compressed. This also determines the power rating (typically in kW or HP) of the air compressor.
For example, a 30 PH (22 kW) air compressor can provide a flow of about 140 cfm (3.96 m3/min) at 102 psi (7 bar g).
A few ways to determine the capacity requirement of a plant are through the OEM recommendation, past equipment experience, or through air audits. Air audits enable companies to get valuable insights into their plant’s compressed air utilization and determine the actual demand. Compressed air experts can chart out a customized and comprehensive energy management plan for your needs through air audits.
Reciprocating compressors are well suited for flow below < 50 cfm. For higher flow capacities, screw compressors are better suited when comparing the two technologies.
Duty Cycle & Utilization
Duty cycle refers to the time a compressor is expected to run in a given hour at full capacity. Reciprocating compressors are designed to operate between 60-80% duty cycles and screw compressors are designed to operate at 100% duty cycle.
Life cycle cost of a compressor constitutes of Initial Cost + Maintenance Cost + Energy Cost.
In a screw compressor, energy cost contributes to over 75% of the life cycle cost over 10 years’ operation time. It is critical to understand the life cycle cost of a compressor before making the purchase decision as cost of ownership varies by technology.
The amount of time a compressor runs in a day influences the energy cost. While looking to select a compressor with optimal life cycle cost, follow these guidelines:
When utilization is < 4 hours/day select a reciprocating compressor
When utilization is between 4 and 8 hours/day, a belt driven screw compressor is preferred
When the utilization exceeds 8 hours/day, a direct driven screw compressor is the best fit.
ELGi has created a helpful product selector to help you explore the air compressor options based on your requirements: https://www.elgi.com/us/product-selector/
Before finalizing your decision, we welcome you to speak to our compressed air experts. ELGi has a network across North America readily available to help you with your purchase process. To find the nearest provider, visit https://www.elgi.com/us/distributors/