What Standards and Certifications to Consider When Selecting an Oil-free Air Compressor?
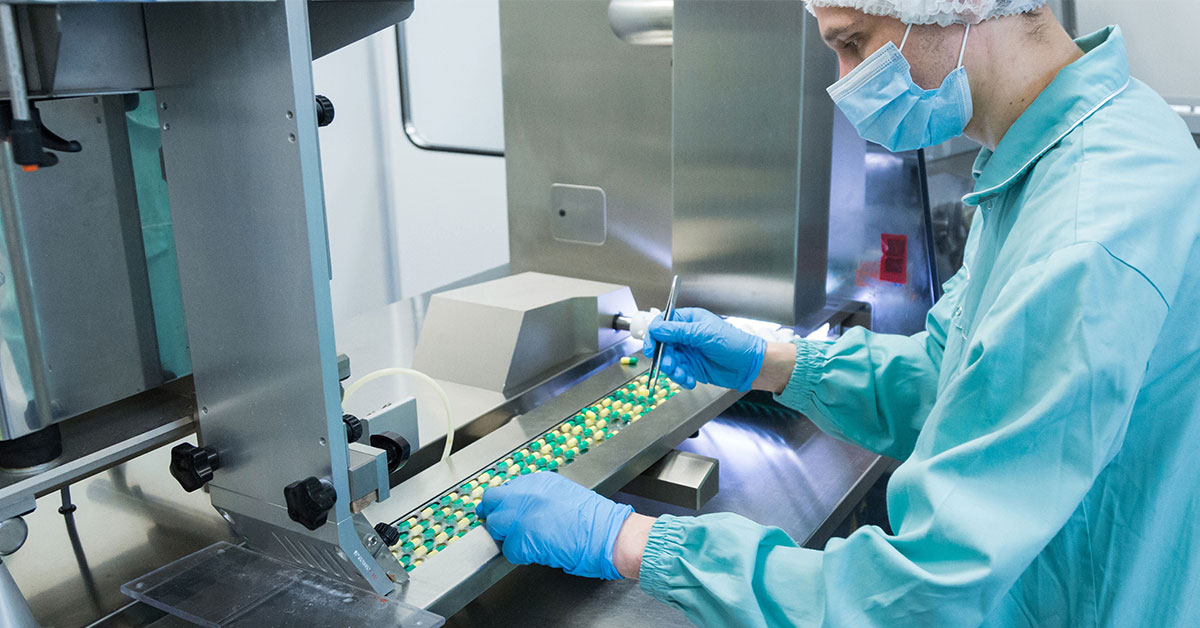
There are many industries where the quality of the compressed air used is of utmost importance. For example, various processes like the manufacturing of pharmaceuticals, microprocessor chips, food and beverage processing, and automotive painting require compressed air that must be free of contaminants. These are industries where the presence of oil, oil vapour, or microbiological contaminants can adversely impact the end product.
Hence, the International Standards Organisation (ISO) has prescribed certifications to help such industries ensure that they select the right air compressor for their applications by ensuring that the air compressor complies with the certified standards. This is why these industries turn to the ISO 8573-1 (2010) certification, with Class 0 standard, which represents the highest air quality attainable.
Use of an ISO 8573-1 certified compressor is the only way to ensure 100% oil-free air for your critical industrial applications. Class 0 compressors offer exceptional reliability, minimal maintenance requirements, and cost-effective operation, making them an excellent investment.
Certified compressor manufacturers like ELGi ensure compliance with relevant industry standards, certifications, and regulatory requirements. ELGi maintains detailed documentation of the air compressor manufacturing process, including materials used, assembly procedures, and quality control checks, meeting industry standard of air purity, such as ISO 8573-1 CLASS 0 and ISO 22000 certification. Adhering to air purity standards, including Compressed Air Standard ISO 8573-7 and ISO 8573-1 purity classes, is essential for delivering quality compressed air.
Why Do You Need to Know Your Air Quality Needs?
Understanding your air quality requirements is crucial for two primary reasons:
- Adherence to specific air quality standards is essential for certain applications.
- Failure to meet these standards can lead to production shutdowns, potential product recalls and eventually reputational damage.
As a general guideline, the higher the required air purity, the more costly it becomes to produce. Achieving extremely pure air necessitates additional equipment like filters and dryers, and the production process also consumes more energy. Therefore, selecting the appropriate purity level can impact operational costs.
A Very Good Start – ISO 8573-1
Several resources are available to ensure your compressed air system and processes meet the desired air quality standards.
The most significant is ISO 8573-1 (ed. 2010), a globally recognised air quality standard that can be structured into seven distinct air quality classes and addresses the three primary types of contaminants. ISO 8573-1 is your essential reference point for determining the required air purity level. It prescribes the maximum allowed contaminant levels for your compressed air system at specific treatment stages.
In some cases, this figure can be quite high. In other cases, the requirements are very stringent. Therefore, to determine your compressed air treatment requirements, your first step is ascertaining the ISO 8573-1 class applicable to your application. As shown in the chart below, the class demanding the highest air quality is Class 0. No defined contamination levels or pressure dew points exist in this situation, but both must be lower than Class 1 standards.
Class | A | B | C | |||
---|---|---|---|---|---|---|
SOLID / DUST Partical in micron | Water @ 7 bar / 100 psi Pressure Devewpoint | OIL (including vapor) | ||||
0.10-0.5 | 05.-1.0 | 1.0-5.0 | Mg / m3 | |||
Max number of particles per m3 | °C | °F | ||||
0 | As specified | As specified | As specified | |||
1 | ≤ 20 000 | ≤ 4 | ≤ 10 | -70 | -94 | ≤ 0.01 |
2 | ≤ 400 000 | ≤ 6000 | ≤ 100 | -40 | -40 | ≤ 0.1 |
3 | - | ≤ 90 000 | ≤ 1000 | -20 | -4 | ≤ 1 |
4 | - | - | ≤ 10 000 | +3 | +38 | ≤ 5 |
5 | - | - | ≤ 100 000 | +7 | +45 | > 5 |
6 | - | - | - | +10 | +50 | - |
ISO 8573.1 2010 air quality classes table
Zero Microbial Contamination – ISO 8573-7
ISO 8573-7:2003 establishes a rigorous test method for discerning viable, colony-forming microbiological organisms such as yeast, bacteria, and endotoxins from other solid particles that may be present in compressed air. As part of a comprehensive series of standards designed to standardize air contamination measurements, this standard outlines a systematic approach for sampling, incubating, and quantifying microbiological particles. This methodology is particularly valuable for determining purity classes in alignment with ISO 8573-1.
ELGi's AB Series oil-free air compressors proudly hold ISO 8573-7:2003 certification, which plays a pivotal role in ensuring contaminant-free compressed air. The adherence to this standard also underscores ELGi’s commitment to delivering compressed air of the utmost quality and purity for your critical applications.
The Benefits of ISO 22000 Certification to the Food Industry
ISO 22000 is vital for maintaining quality and transparency in food production and processing facilities. The three main safety challenges present in the food and beverage manufacturing industry—physical, chemical, and biological hazards—are the focus of this standard. The essential elements of ISO 22000 certification are designed to manage and mitigate these hazards effectively. The process of obtaining ISO 22000 Certification involves:
- Establishing a documented food safety management system to oversee operations throughout the facility.
- Implementing prerequisite programs to ensure the maintenance of a sanitary environment.
- Adopting the Hazard Analysis Critical Control Point (HACCP) principle, which identifies, prevents, and eliminates hazards in the food production process.
ELGi's production facility is ISO 22000 certified (Food Safety Management System – FSMS), confirming its plant, and hence the oil-free air compressors manufactured in the plant meet the most stringent food and beverage industry requirements.
ELGi's food-grade certified compressed air solutions are designed from the ground up to offer efficient, contaminant-free air to food manufacturing processes. With the ISO 22000 certification awarded to our manufacturing plant, we provide our customers with an additional layer of reassurance, ensuring consumers are getting food they can trust.
Choosing the Right Oil-Free Air Compressor for Your Applications
ELGi is a leading compressed air manufacturer offering compressed air solutions that provide zero risk of contamination with improved energy efficiency and long-term reliability to meet the sensitive needs of a diverse range of industries such as pharmaceuticals, food and beverages, electronics, and automotive where any chance of oil contamination in the production processes cannot be tolerated.
Class 0 Oil Free Air Solution
ELGi's Oil-free air compressors have consistent oil-free air, meeting ISO8573-1 class 0 oil standards. Our compressors come with a food-grade coating where air contacts the metal surface inside the compressor, ensuring consistent oil-free air without metal debris. In addition, pipes with special e-coating and optimised rotor clearances provide clean, oil-free air delivery.
Reduced Cost of Ownership
Oil-free air technology from ELGi improves productivity by eliminating energy waste caused by pressure drops. Additionally, our oil-free air compressor range, the AB Series and the OF Series, are designed to allow for easy component access, minimising the time and cost associated with maintenance.
Distinctive Design and Ownership of Technology
ELGi is among the few global air compressor manufacturers to design and manufacture oil-free air ends. Our air compressors incorporate our proprietary oil-free technology that are meticulously engineered to provide unparalleled uptime and reliability. Additionally, the distinctive η-V rotor design by ELGi optimises the compressed air system by minimising pressure losses and maximising stage efficiency. ELGi regularly evaluates and improves air compressor manufacturing processes and designs to stay competitive and to meet evolving customer demands.
Highest Efficiency and Reliability
Our air end rotors and housing are coated with a PTFE-based, food-grade coating, designed to withstand corrosion and endure temperatures of up to 250 degrees C. This ensures long-term performance with best-in-class efficiency.
Reduce Environmental Footprint
Utilising ELGi's oil-free air technology not only protects end-products for your customers but also reflects your commitment to environmental sustainability. Leaks and energy waste are minimised. Also, the need for condensate treatment is eliminated. As a result, you safeguard the environment and enhance your adherence to international regulatory standards. When it comes to ELGi's air compressor manufacturing processes, ELGi emphasizes the selection of high-quality materials for all components. ELGi prioritizes the use of corrosion-resistant materials that are perfectly suited for the environment in which the ELGi air compressor will operate.
ELGi's oil-free compressors are certified to meet ISO 8573-1 Class 0 standards. This is the highest level of air purity, ensuring that the compressed air is free from oil and other contaminants, making it safe for critical applications such as pharmaceuticals, food processing, and electronics manufacturing. In addition, ELGi also offers oil-lubricated compressors that adhere to industry standards and certifications, including ISO 9001, to ensure the quality of the manufacturing process and the reliability of the equipment.
Contact our experts if you need additional information on ELGi's oil-free compressors or more help determining the air quality class for your critical industrial applications. Our team of experts is here to provide you with not just information but tailored solutions that ensure your operations are backed by cutting-edge, contaminant-free compressed air, ensuring best-in-class performance and efficiency. We value your success, and our specialists are ready to guide you towards achieving air quality excellence.
RELATED BLOGS
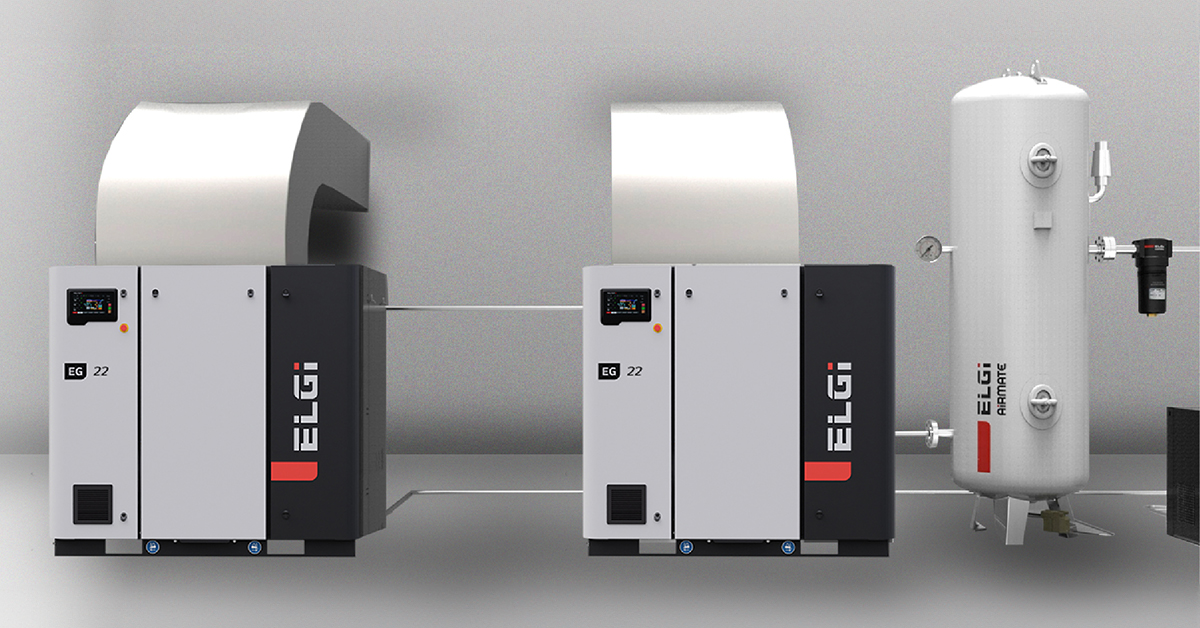
Understanding the importance of a well-sized compressed air system In industrial envir...
Read More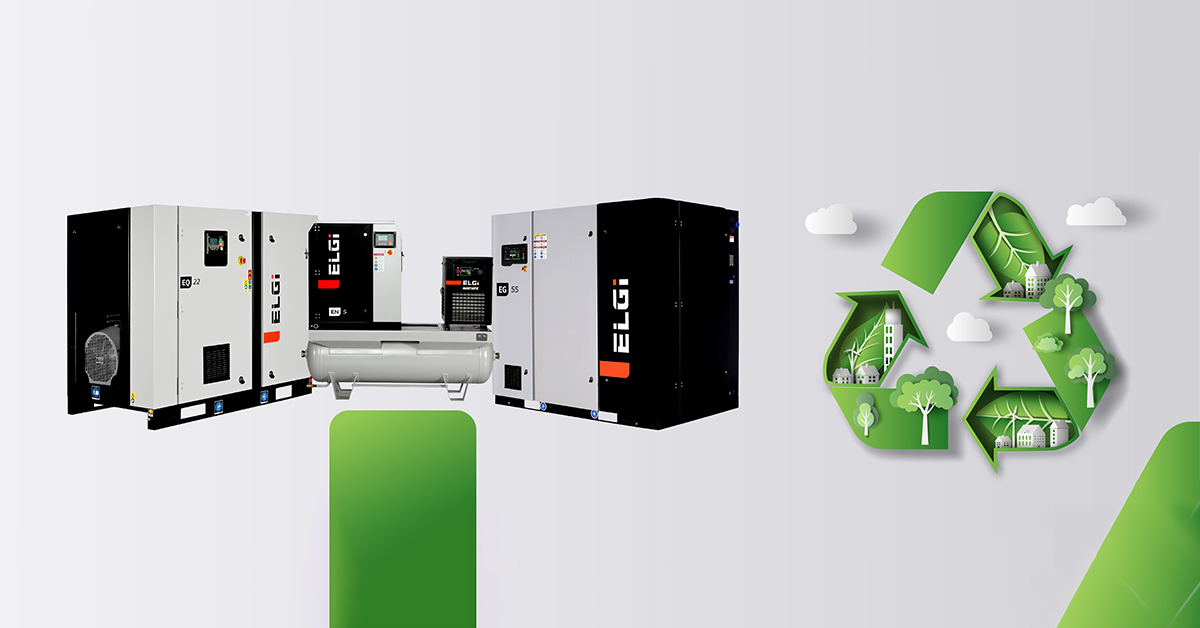
In today’s times of heightened environmental consciousness among businesses, the signifi...
Read More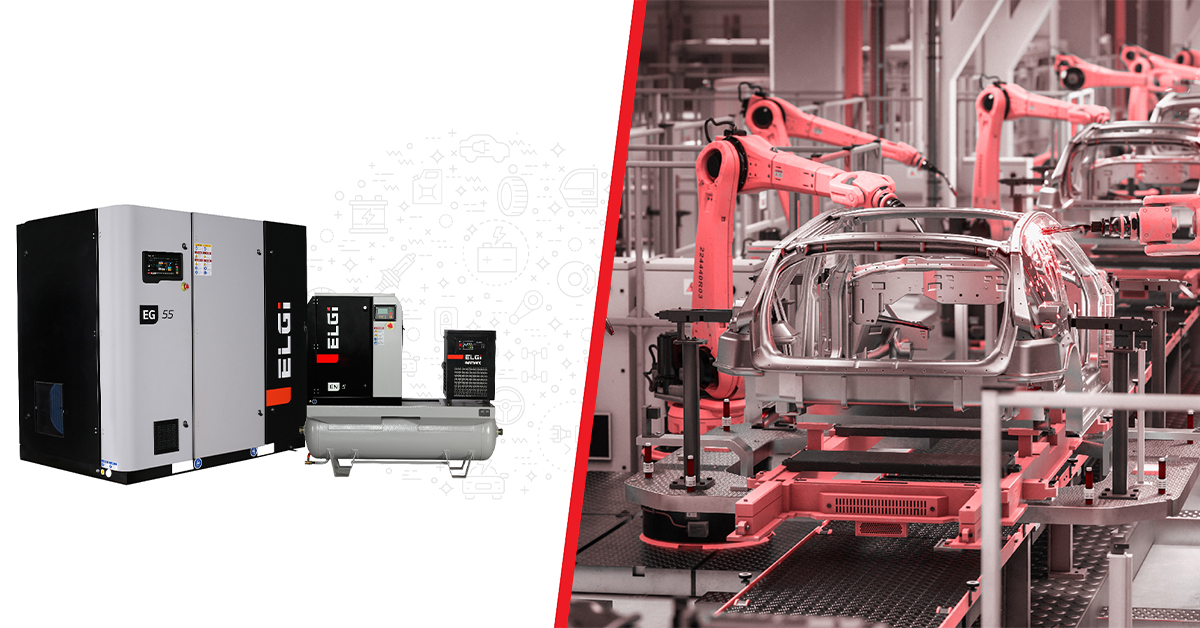
Over the past decade, there has been a notable surge in the global automotive manufacturin...
Read More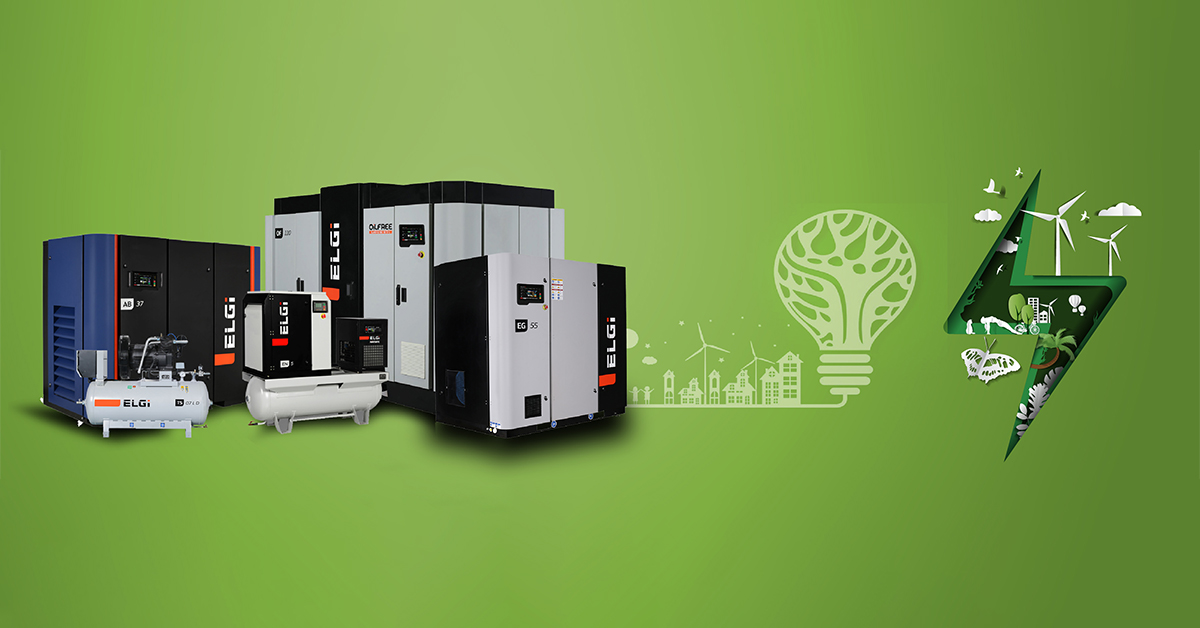
In today’s times, where sustainability and energy efficiency are not just trending terms...
Read More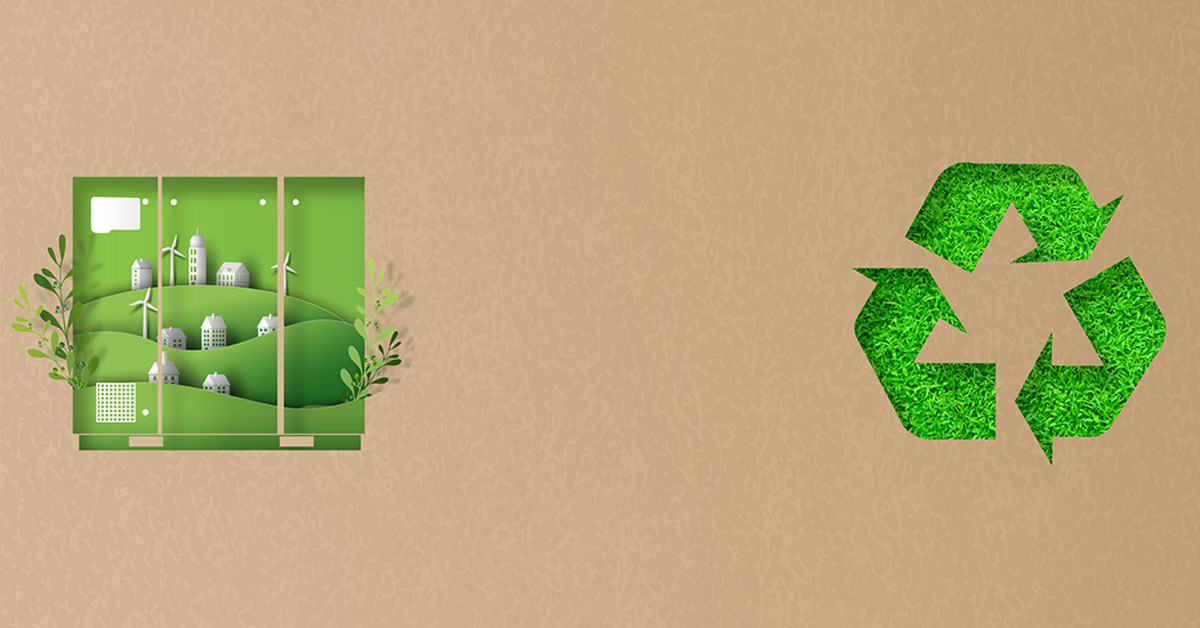
Imagine a busy world of factories and machines, always changing to be more efficient and k...
Read More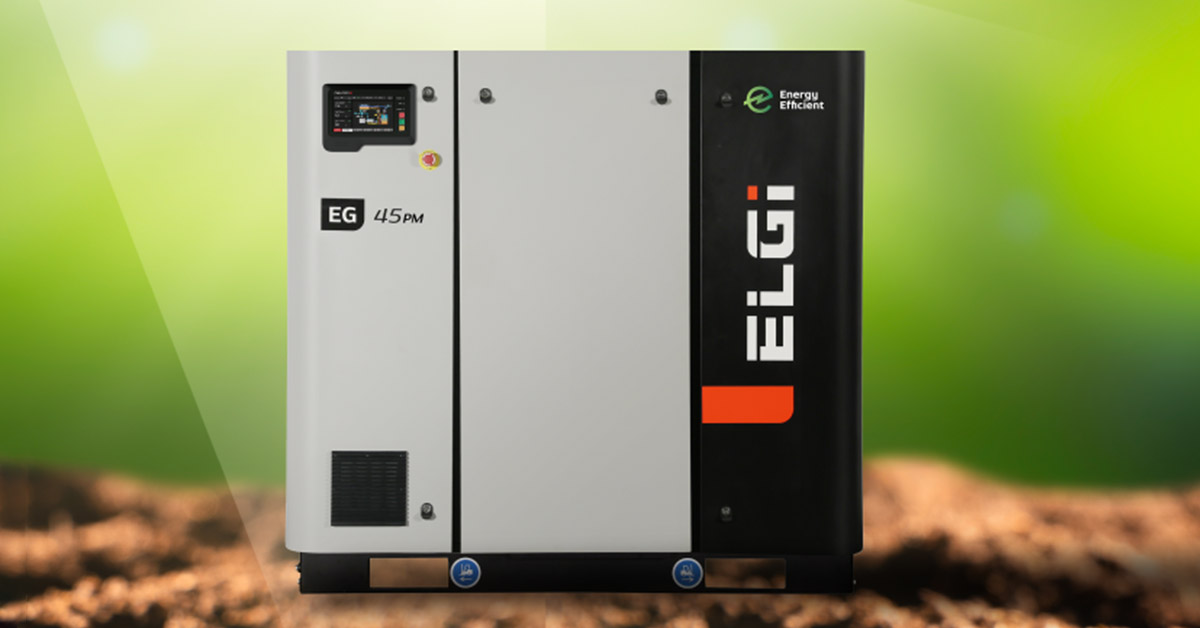
The critical role of energy efficiency In today's industrial landscape, energy efficien...
Read More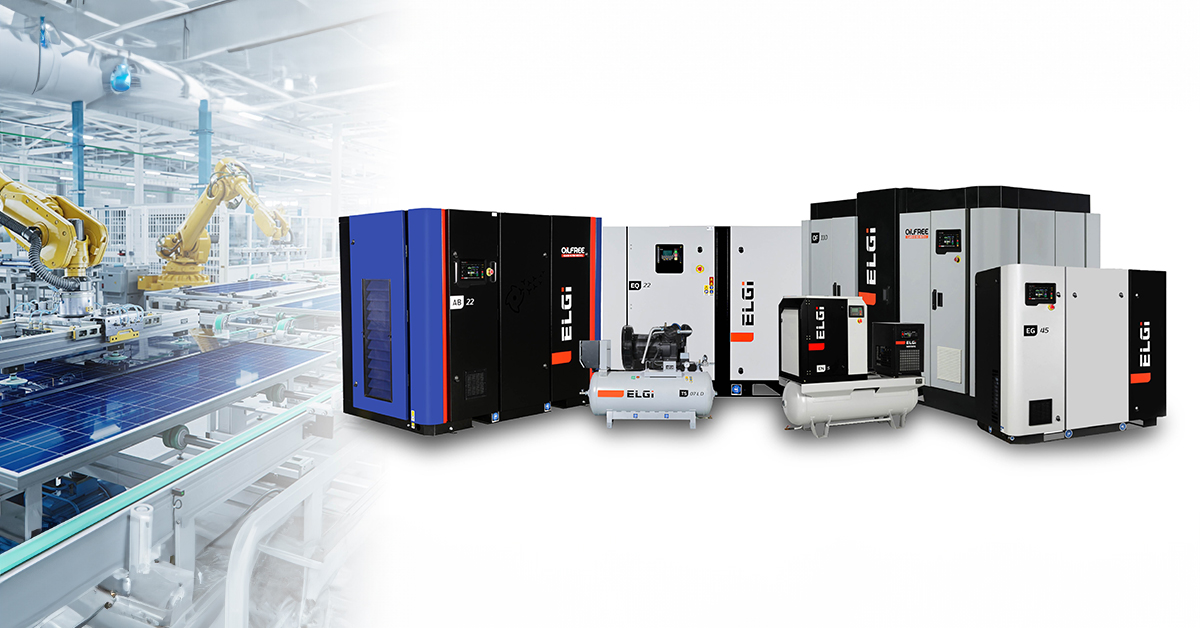
The Essential Role of Air Compressors for Manufacturing in Modern Industries Air Comp...
Read More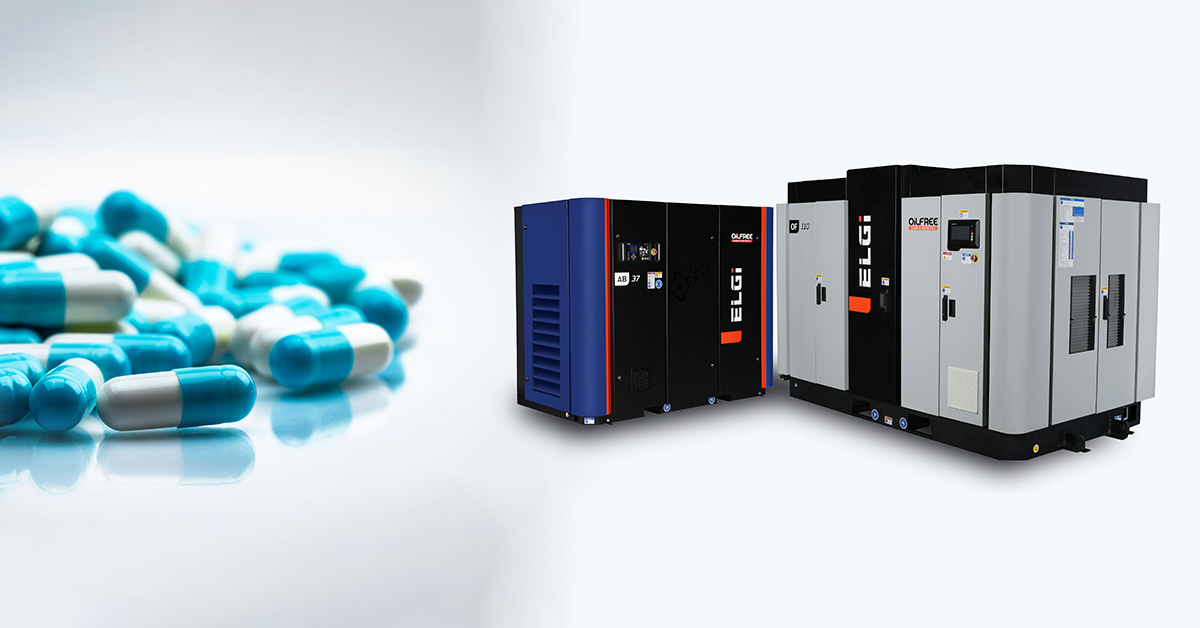
A Closer Look at Compressed Air in Pharma In the pharmaceutical industry, the spotlight...
Read More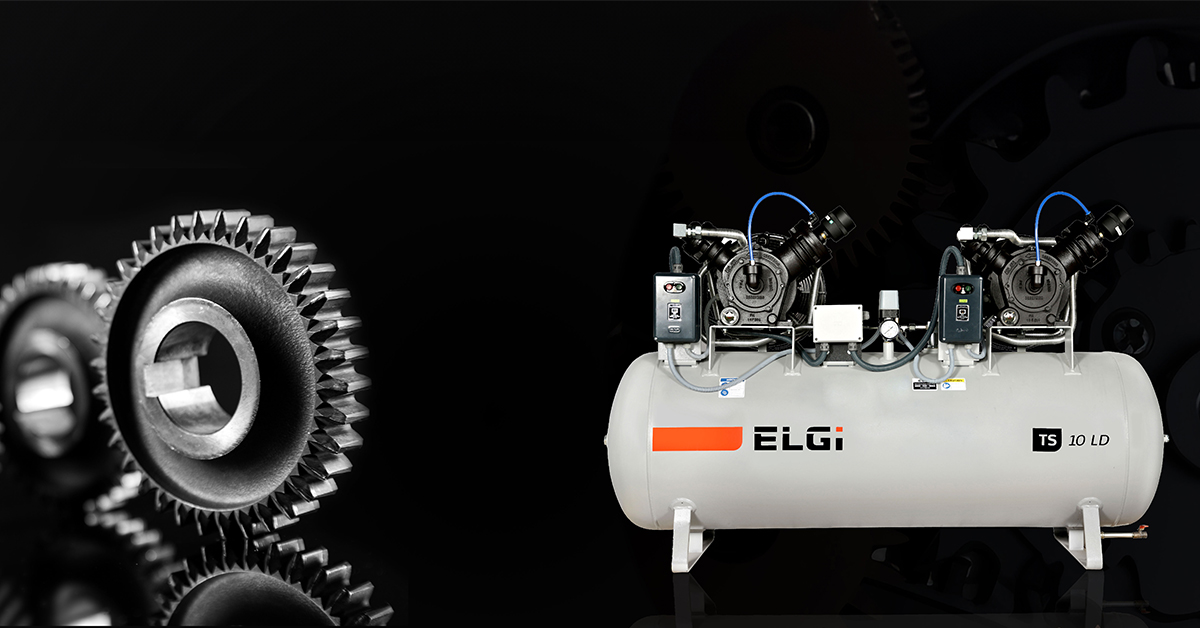
Reciprocating air compressors, also known as piston air compressors, are widely used acros...
Read More
One of Europe's leading composite tooling solutions providers raises the bar on precision ...
Read More