VARIABLE FREQUENCY DRIVE VS FIXED SPEED DRIVE
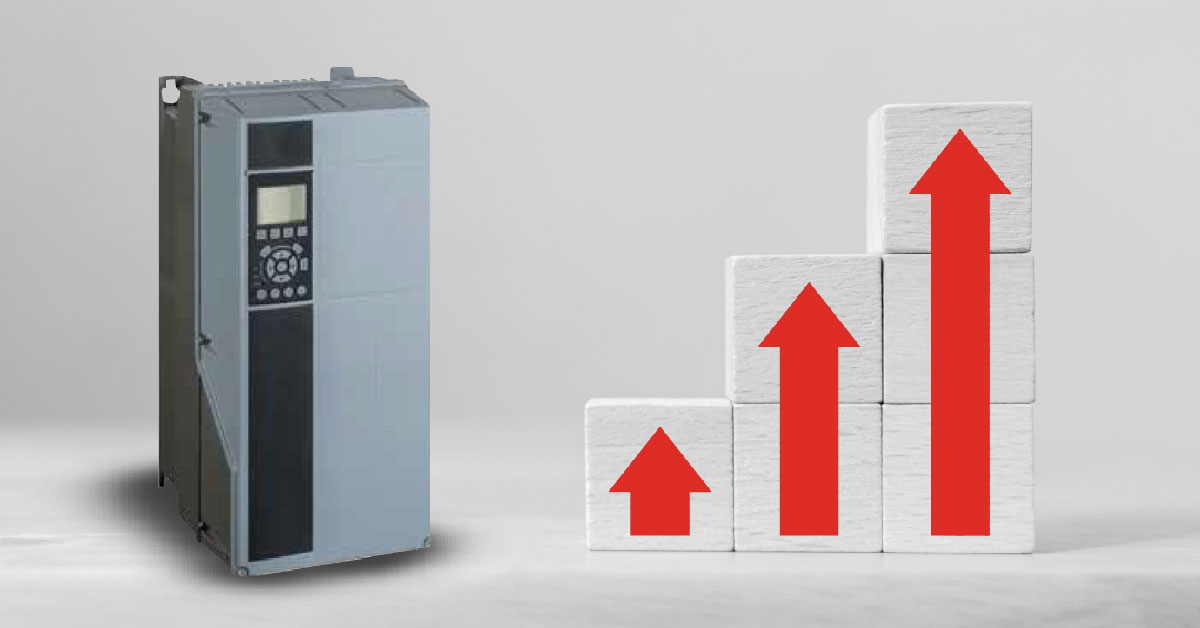
Today, businesses are looking for sustainable manufacturing practices and are adopting processes and techniques that minimise negative environmental impacts while conserving energy. Manufacturing companies in industries like pharmaceuticals, automotive, food and beverage, textiles, and others are opting for energy-efficient solutions with low operating costs, leading to high productivity.
Different industries are powered by various pneumatic applications that demand a specific airflow (m3/min). Selecting a suitable compressed air system is crucial to ensure that the air compressor meets the airflow and pressure demands of the pneumatic applications while ensuring optimal performance.
Customers can choose from ELGi’s wide range of air compressors equipped with or without a variable frequency drive based on the variation in airflow demand, for their industrial requirements. In the case of a fixed speed air compressor, the compressor runs at the same rate, consuming the fixed power for the air demand. The electrical motor runs at the maximum constant speed irrespective of the compressed air requirement. On the other hand, the variable speed air compressors can automatically adjust the speed between its minimum and maximum range, ensuring that the compressed air generation matches the compressed air demand and subsequently consumes significantly less energy at low demand.
Overview of fixed speed and variable speed technologies
There are two main types of speed control for electric motors: fixed speed and variable speed. Fixed speed means that the motor will run at a constant speed, regardless of the load or demand. This is the most common type of speed control used in applications that demand constant speed. Variable speed means that the motor will adjust its speed according to the load or demand. VFD is useful in applications where energy efficiency is a priority while ensuring that the compressed air generated matches the end application's demand. In oil-lubricated and oil-free compressor models, variable frequency drives are commonly used in rotary screw air compressors.
There are several ways to achieve fixed speed control. One of them is the start/stop control. In this case, a pressure switch sends a signal so that the compressor starts when the pressure goes below the required value and stops when the value reaches the maximum set value. The compressor thus either operates at full load or not at all.
Another option is the load/unload control. Load/unload control is used often in medium-sized compressed air applications with higher running hours. Instead of stopping the motor of the compressor, the compressor is put in unload, meaning that there is no airflow provided, just a small quantity of air to keep it running. In unload mode, the compressor consumes around 30% of the full load consumption while not providing any airflow. This is to guarantee that the compressor can be used at any time at full load.
The last option is modulation, which is ideal for a limited variation in compressed air flow. The inlet valve can modulate the flow depending on the pressure of the compressed air system. Throttling or closing the inlet valve results in a reduction of the compressed air flow of the compressor. The compressor can therefore adjust the flow from 100% to about 50% of the rated capacity. In case of a lower demand, the compressor will switch to the load/unload control.
Pros and cons of fixed speed and variable frequency drive air compressors
Fixed speed air compressors deliver a constant maximum airflow. Therefore, they benefit applications that have continuous fixed airflow requirements for operations. Fixed speed drives are typically more maintenance friendly and reliable as they require less cooling. However, Fixed speed air compressors are less efficient at times when the compressed air demand is lower as they cannot adjust speed as Variable frequency drive air compressors.
The variable speed air compressors are suitable for varying airflow demands. A variable speed compressor is ideal for fluctuating airflow demands anywhere between the compressor's minimum and maximum airflow capacity. The VFD air compressors will adjust the motor speed and ensure that the compressor does not consume excess energy by running at maximum capacity. Air compressors with VFD can save significant energy costs compared to fixed-speed units.
Why variable speed is not always the right choice
Although a variable speed drive compressor may be more energy efficient than a fixed speed air compressor, it is not always the right choice. A variable speed drive compressor will result in a 2-4% efficiency loss in applications where the air demand is constant. In addition, the variable speed drive system can lead to higher maintenance costs. For these reasons, a fixed-speed compressor is usually the better choice in applications where the air demand is constant.
When variable speed drive is the right choice and why?
Opting for a variable frequency drive air compressor depends on the end application's airflow (m3/min) demand. The variable speed air compressors are more appropriate when the end application has varying airflow demands and an irregular duty cycle. Enhance the air compressor operations with variable speed air compressors, designed to deliver efficient, reliable, and cost-effective compressed air solutions. Embrace technology that not only fulfills your current needs but also adapts seamlessly to future demands. ELGi’s compressed air systems with VFD can operate at various speeds to match the application's air demands, saving significant energy costs. In addition, the variable frequency drive air compressor can be started and stopped as needed, which further reduces energy consumption.
VFDs are commonly used in oil-lubricated or oil-free rotary screw air compressors to control the speed of the motor, which in turn affects the amount of air delivered by the air compressor. Reducing motor speed allows VFDs to reduce energy waste in screw air compressors.
Why Compressor sizing remains important?
With so many air compressor technologies in the market today, the right selection for your production can be overwhelming. When choosing an air compressor, assessing the load type is critical. Once making the air compressor selection for your facility, some key considerations are duty cycle, operating pressure, and airflow demand.
Here are some points for consideration when choosing a suitable air compressor for your business.
Airflow requirements: Airflow is the air volume produced by the air compressor at a certain pressure in a given amount of time. Before the compressor selection, it is crucial to determine how frequently the tasks need to be carried out or how many jobs are performed simultaneously to calculate the total airflow requirement for all pneumatic applications. Selecting an underpowered air compressor would mean that the air compressor cannot supply the required flow and pressure for the pneumatic applications which could lead to problems in the production line.
Pressure requirements: Pressure (barg) is the force required to perform a task at a given time. It is ideal to select the compressor basis the working pressure needed to operate the pneumatic applications. If an air compressor is operated at a higher pressure than required, it will consume significantly more energy to achieve that additional pressure rating.
Duty Cycle: The duty cycle refers to the operation cycle or the time the compressor runs to provide compressed air at a consistent pressure and specific flow rate. This is one of the critical parameters which helps decide if a fixed speed drive or a variable frequency drive (VFD) is required.
Additionally, we recommend to conduct an ELGi Air Audit with one of our compressed air experts to determine the right air compressor for your application and requirements.
Why should you opt for ELGi's variable frequency drive air compressors?
Here are a few reasons to consider ELGi air compressors with variable frequency drive for your applications:
Energy-efficiency: In ELGi air compressors with variable frequency drive, the speed of the motor is regulated, ensuring the required airflow is produced, and no energy is wasted. The VFD air compressor greatly benefits industries and applications with varying airflow (m3/min) demands.
High Uptime: The regulated compressed air supply helps optimise the compressed air system and reduces the chances of equipment wear, thus offering higher uptime.
Energy consumption amounts up to 75% of the total lifecycle cost of an air compressor and is a significant factor in managing the operating costs. Organisations across the globe are looking for ways to minimise operating costs to stay profitable and reduce their impact on the environment. Variable frequency drive (VFD) enabled air compressors offer the opportunity to manufacturing and service companies looking for energy-efficient solutions and high profitability to significantly optimise their productivity and energy consumption.
ELGi offers its customers a wide range of compressed air solutions, from fixed speed to variable frequency drive enabled rotary screw air compressors depending on the end-use application demands.
Our compressed air experts can help you select the right air compressor for your application. Contact us at [email protected].
Frequently Asked Questions (FAQs)
How do I check the potential for energy savings through a Variable Frequency Drive (VFD)?
Every air compressor is equipped with a controller. This controller shows the running hours as well as load and unload hours. If the data shows the unload hours to be 15-20 percent of total running hours, there is a significant potential to save energy through a VFD.
How do I identify the air compressor which is required for VFD retrofitting?
If you’re using only one air compressor to provide the airflow as per demand, the VFD can be retrofitted to the same compressor (if the potential in saving has been identified). Whereas, if your facility has employed multiple air compressors to support the airflow (m3/min) demand, verify the base load and trim load requirements to choose the best possible compressor for retrofit. ELGi offers technical consultation to identify potential savings in your compressed air system, contact our experts.
How does one confirm the base load and trim load requirements of a rotary screw air compressor?
The best method to ascertain the base load and trim load requirements of a rotary screw air compressor is to conduct an energy audit from a qualified ELGi air expert. They will help you in the measurement of the base and trim load demand accurately.
What will happen if we install a VFD for base load requirements?
Installing a VFD for the base load alone, will not offer any energy saving since the base load does not go to an unload cycle. A VFD-powered machine will consume around 103% at full load (3% VFD losses). Hence there will not be any savings.
RELATED BLOGS
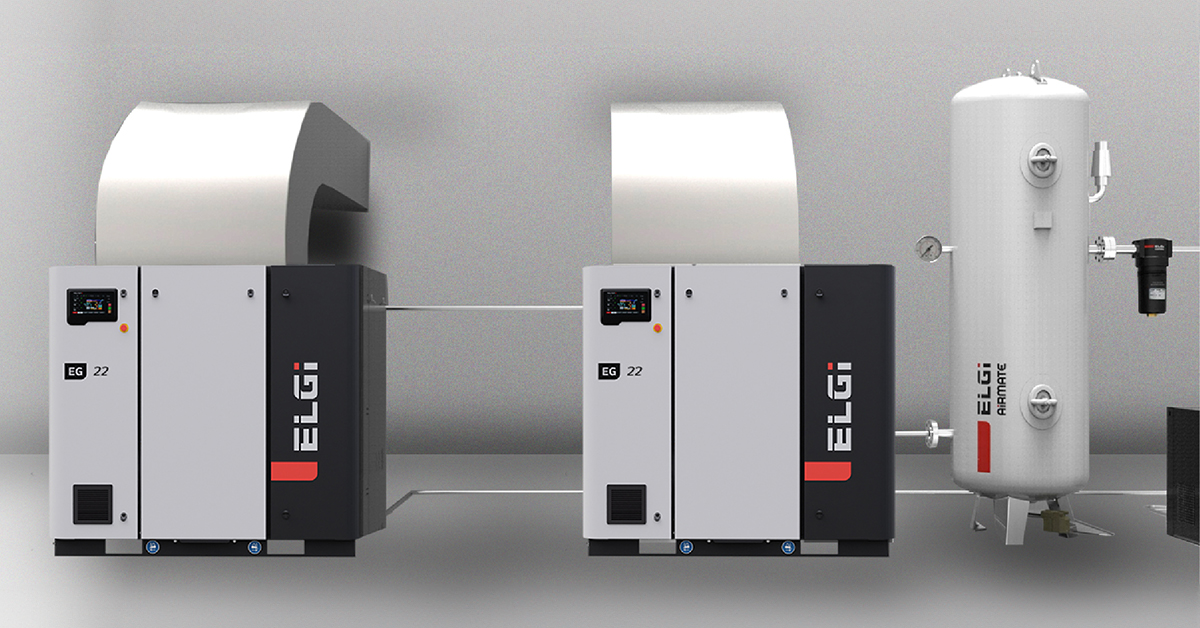
Understanding the importance of a well-sized compressed air system In industrial envir...
Read More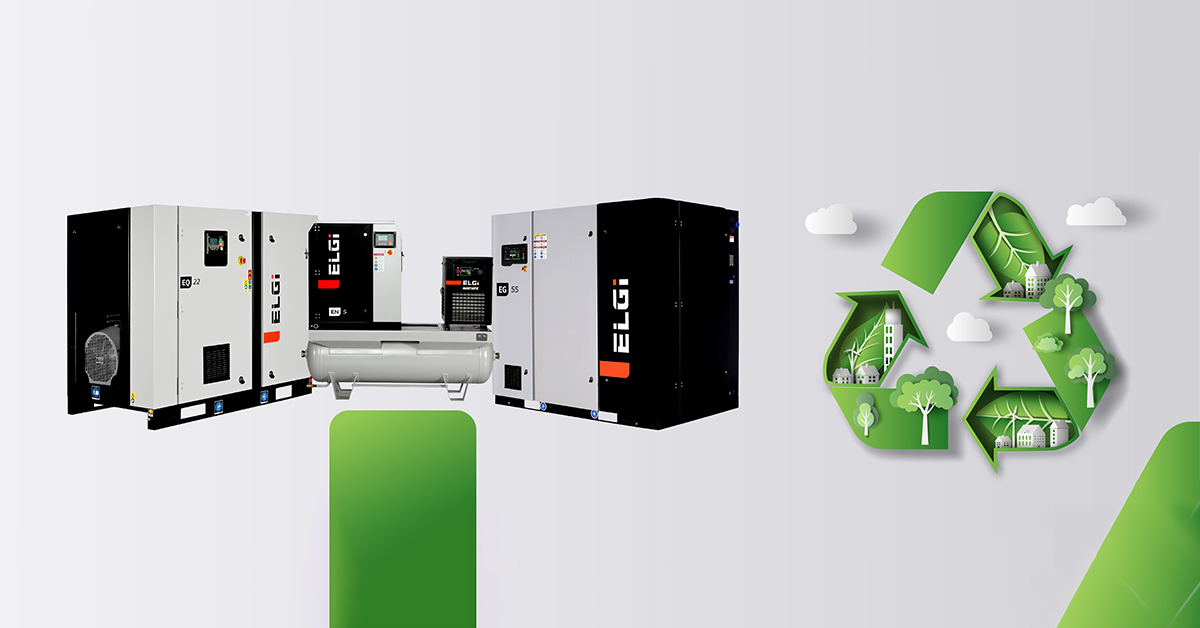
In today’s times of heightened environmental consciousness among businesses, the signifi...
Read More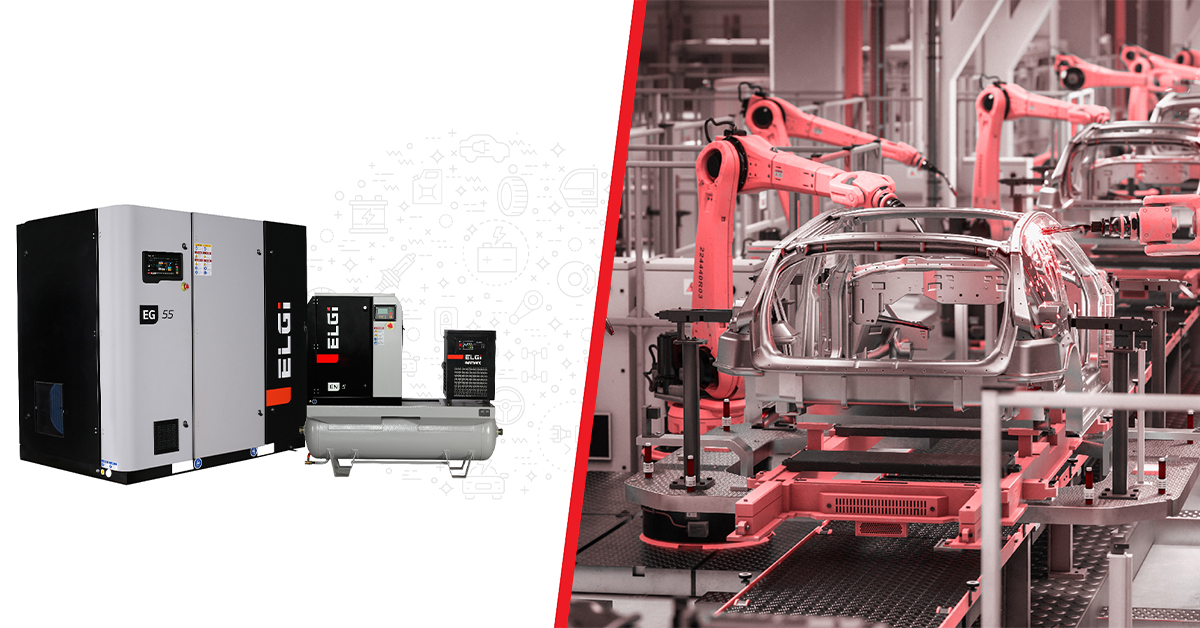
Over the past decade, there has been a notable surge in the global automotive manufacturin...
Read More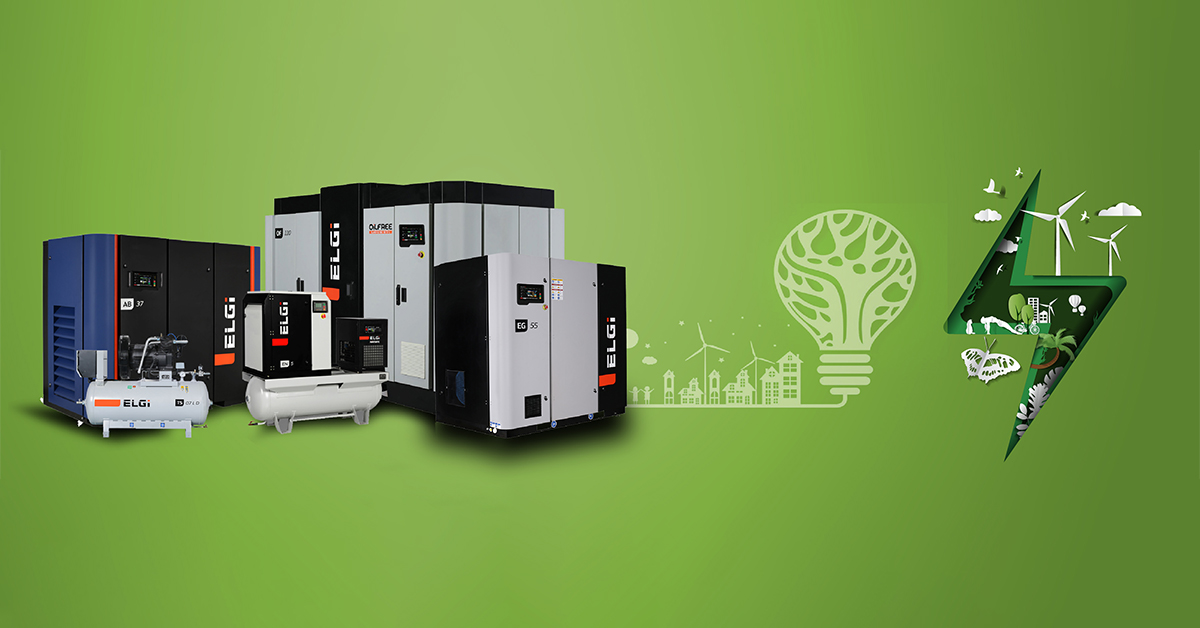
In today’s times, where sustainability and energy efficiency are not just trending terms...
Read More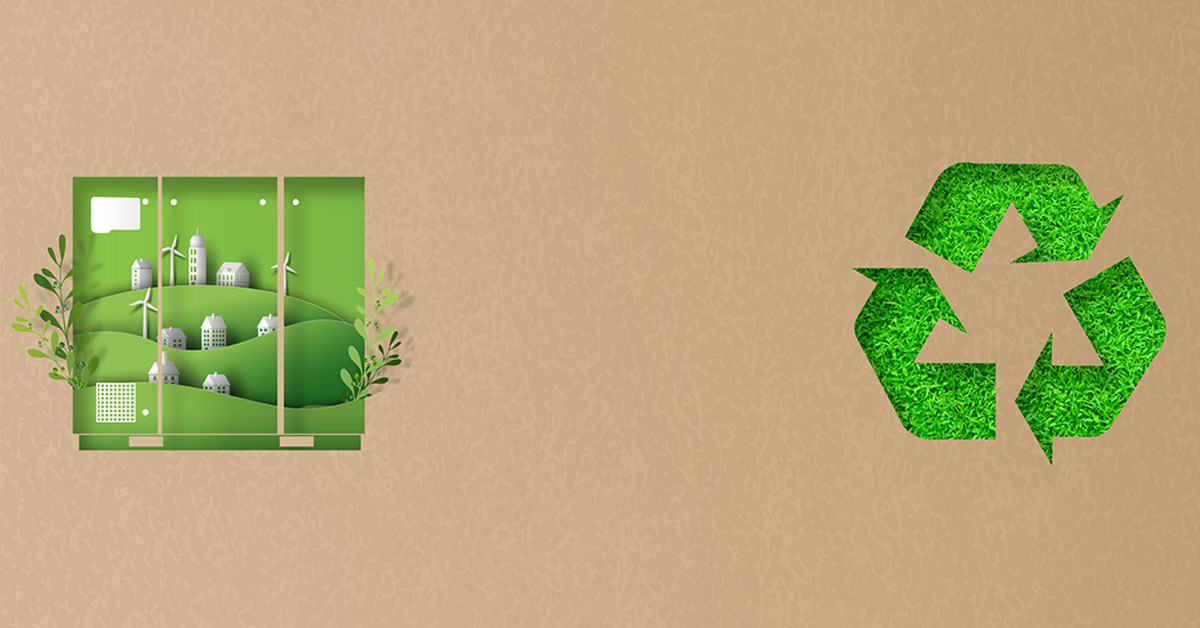
Imagine a busy world of factories and machines, always changing to be more efficient and k...
Read More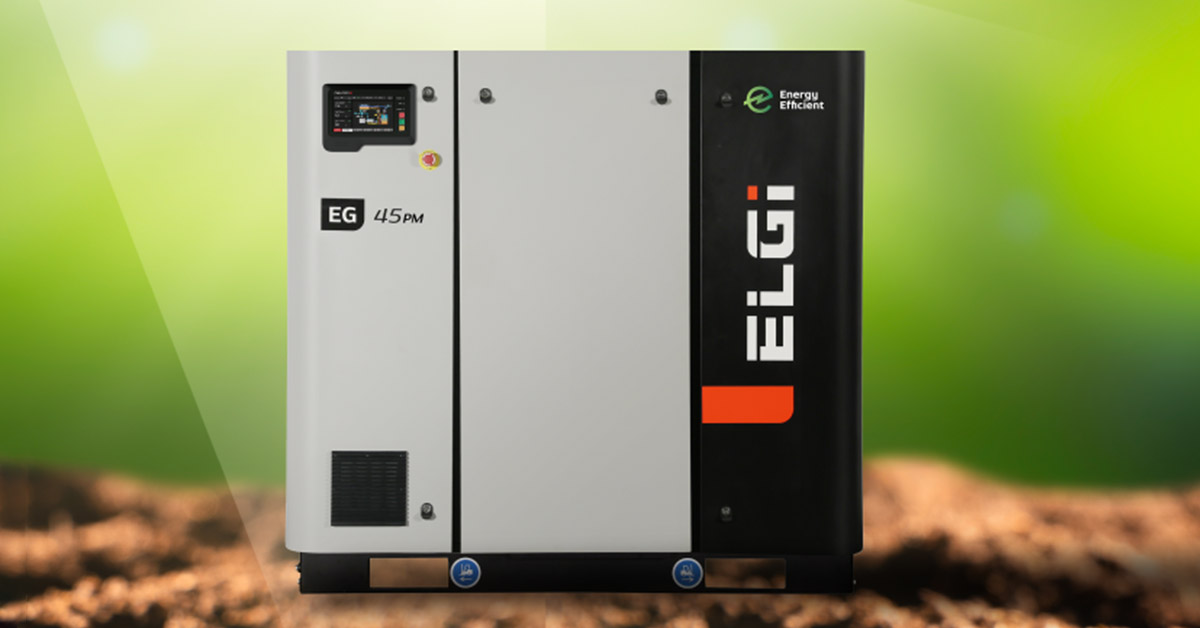
The critical role of energy efficiency In today's industrial landscape, energy efficien...
Read More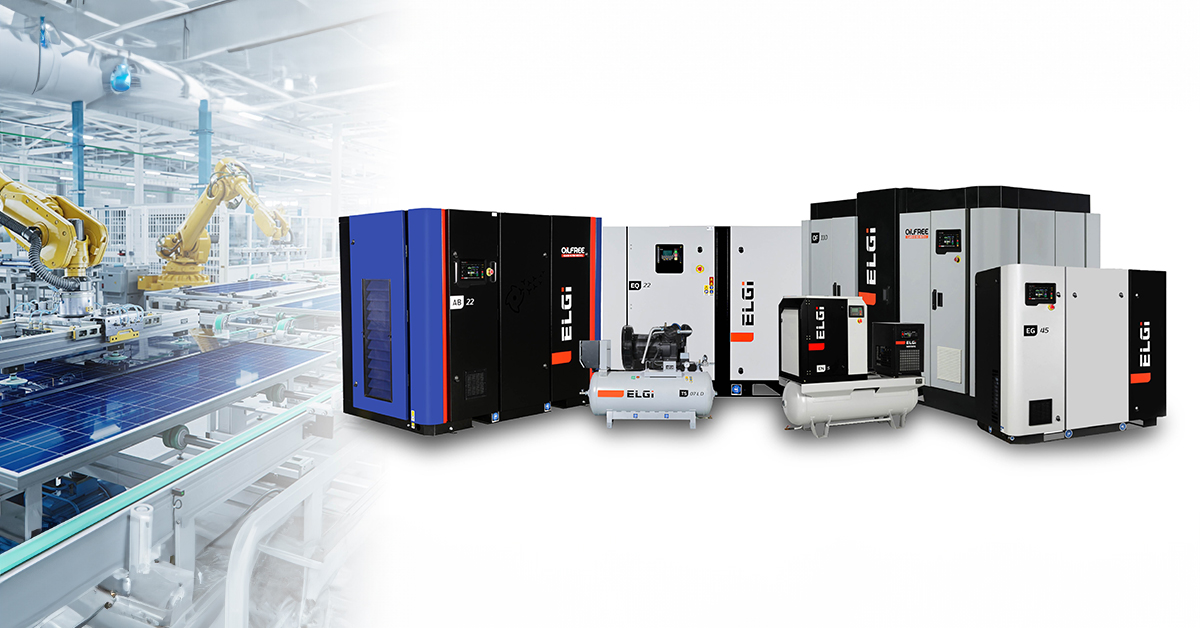
The Essential Role of Air Compressors for Manufacturing in Modern Industries Air Comp...
Read More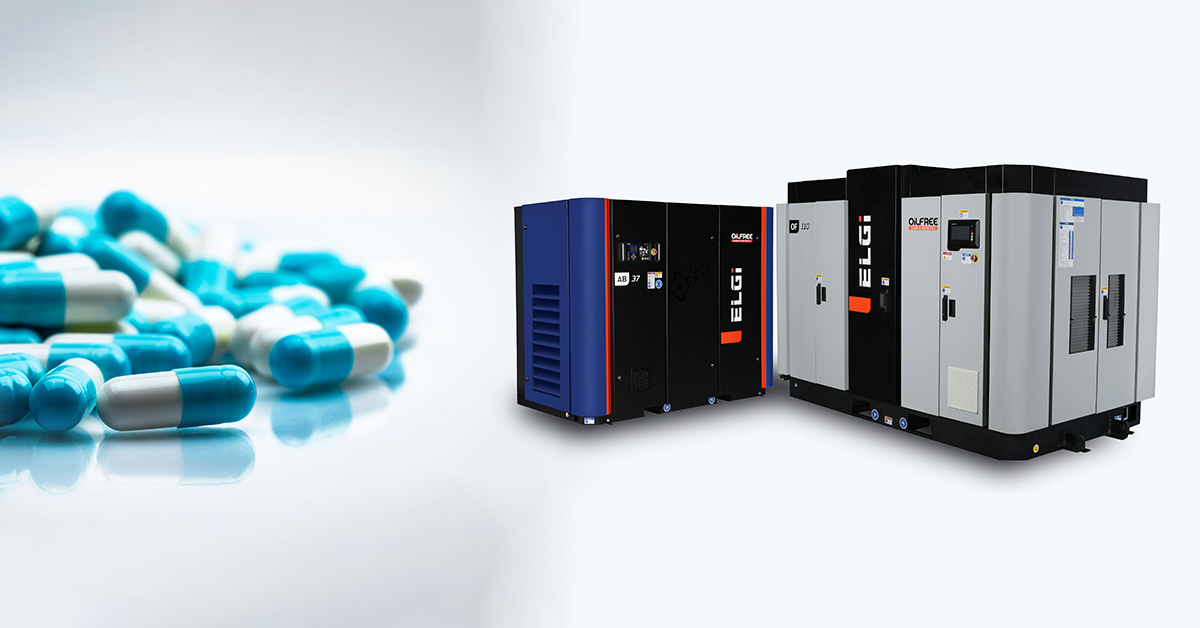
A Closer Look at Compressed Air in Pharma In the pharmaceutical industry, the spotlight...
Read More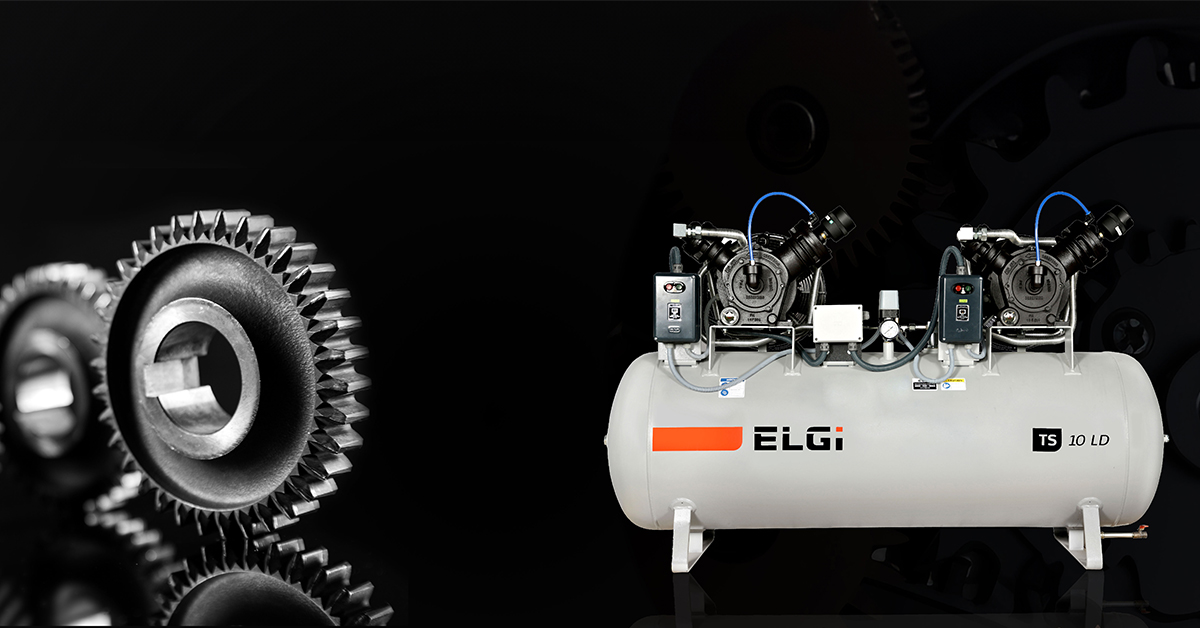
Reciprocating air compressors, also known as piston air compressors, are widely used acros...
Read More
One of Europe's leading composite tooling solutions providers raises the bar on precision ...
Read More