Untapping The Potential Of Industrial Waste Heat Energy
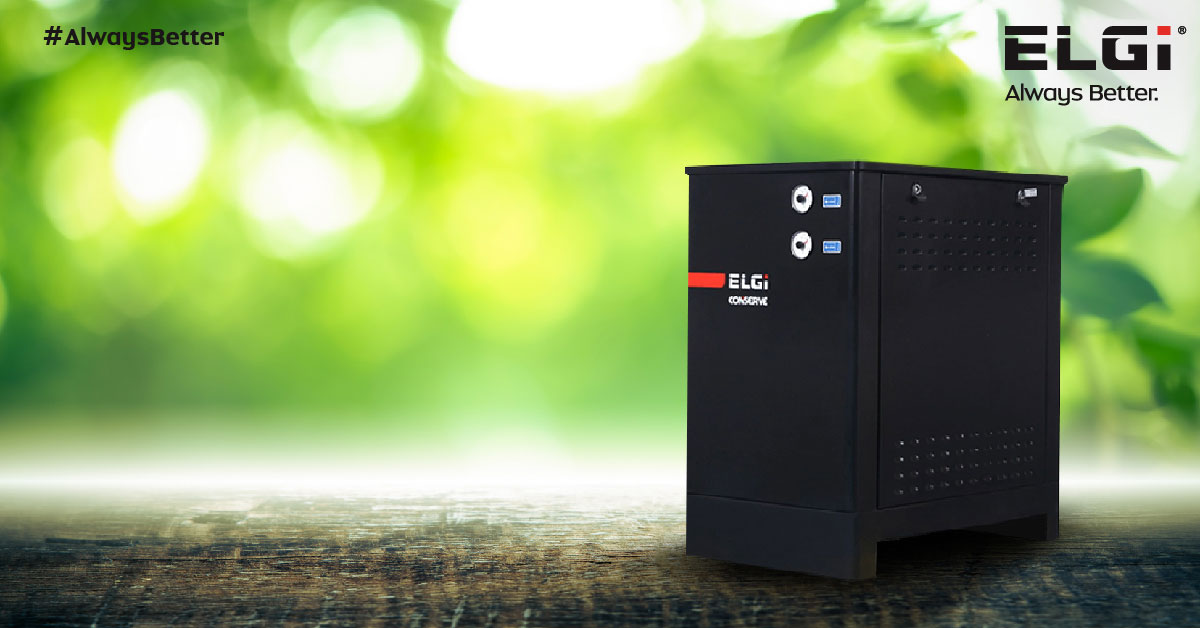
Operations of all sizes now have the tools required to improve energy efficiency and utilise heat from their compressed air systems.
Author: David De Pril, Head of Product Management and Marketing, ELGi Europe
Why aren’t more small and medium-sized manufacturing operations recovering the heat from their compressed air systems? Why has the usual ‘trickle-down’ effect from larger operations taken so long? The potential in energy savings is obvious. The emission reduction benefits are clear and the return on investment (ROI) is high in a short span of time. All the talk is of energy efficiency and waste reduction or elimination – and for a good reason too! It is estimated that the industrial sector in the European Union is responsible for 20 to 25% of the total energy consumption. Industries that prioritize energy efficiency contribute to environmental sustainability and meet regulatory requirements for emissions reductions. Energy-efficient compressors are often equipped with advanced control systems that allow for precise monitoring and management of compressed air production. This helps industries optimize their energy use in different ways. If the EU wants to achieve carbon neutrality by 2050, a huge and largely untapped opportunity lies in industrial energy efficiency and waste elimination. Regardless of the continued 'Force Majeure' clause, eliminating waste energy is not only the right thing to do but makes good business sense too – no matter the size of your operations.
The writing is proverbially on the factory wall. In this article, I will attempt to illustrate the significant advantages of Heat Recovery Systems (HRS) for small and medium-sized manufacturing operations.
How much heat are we talking about?
In a typical oil-injected compressed air system, the theoretically recoverable heat through compressor heat recovery is approximately 96% of the overall electrical energy consumption. It consists of heat dissipated in the oil cooler (78%), the aftercooler (13%), and the heat radiated from the drive motor (5%).
The heat dissipated by the oil cooler can be used for heating water and heat dissipated by the aftercooler and drive motor can be used for supplemental space heating. Compressor heat recovery systems are designed to capture and reuse the heat generated during the compression process. The remaining 4% of heat cannot be recovered since 2% radiates through the canopy and the other 2% vents inside the canopy. Energy-efficient air compressors typically generate less heat, which can be crucial in industries with temperature-sensitive processes or equipment.
There is no one-size-fits-all approach for heat recovery. Compressor Heat Recovery should be part of an overall energy management strategy for a facility. A heat recovery system in an oil-lubricated compressor can significantly improve overall energy efficiency and sustainability by harnessing and repurposing the heat generated during compression. Heat exchangers are commonly used in Compressed Air Heat Recovery systems to transfer heat from compressed air to other mediums like water or air. Factors such as the placement of the air compressor to the process heat, hot water, or air system plays a significant role, but so does the type of compressor running. Oil-lubricated compressors are by far the most commonly used compressors in industrial applications, due to the technology acceptance and reliability. Oil-lubricated compressors can maintain more stable operating temperatures. This, in turn, improves overall compressor efficiency. When compressors operate at cooler temperatures, they consume less energy to achieve the desired level of air compression. It is estimated that 90+% of all screw air compressor installations in Europe are oil-lubricated. They provide a variety of industries, such as automotive, general manufacturing, and packaging, with reliable compressed air. To help the majority of industries, the heat recovery system for air compressor works well together with all oil-lubricated air compressors. A heat recovery system for oil-lubricated compressors is a sustainable and cost-effective solution that not only reduces energy consumption and operating costs but also supports environmental goals. Heat Recovery Systems for Air Compressors contribute to environmental protection by reducing greenhouse gas emissions associated with conventional heating methods. It allows industrial facilities to maximize the value of their air compressor systems while contributing to overall energy efficiency and conservation efforts.
From the beginning
Using waste energy is of course not a new concept. For decades, energy savings were recognised by various industries where the immediate payback from a small initial investment was clear. The most expensive component in the total cost of compressed air is energy. In fact, over the lifespan of a typical compressor, energy typically costs several times more than the purchase price of the compressor. The bottom line, maximizing energy efficiency saves you money. Large operations in the industrial sector were some of the first movers - with operations involving large capacity compressed air systems, running 24/7, and requiring process heat in their operations. Such industries included food and beverage, pharmaceutical, and textiles sectors. Simply put, the larger the scale of operations, the higher the energy savings.
At the same time, small engineering firms were transforming or creating spin-off companies which are also known as Energy Services Companies (ESCOs). Their bread and butter is a broad range of energy solutions including designs and implementation of energy savings projects, retrofitting, energy conservation, energy infrastructure outsourcing, power generation and energy supply, and risk management.
However, the adoption of HRS among small and medium-sized operations has been quite low. The European Commission, in its report on ‘Waste Heat Valorisation: improving energy efficiency in process industries’ noted that “Industrial waste heat recovery potential is still untapped due to several technical and non-technical barriers. Among them, the need for efficient and cost-effective technologies to recover heat losses and to re-use, upgrade or transform this heat for its valorisation.”
Heat Recovery Uses
As mentioned earlier, those operations that gain the most from heat recovery are typically those that also require process heat and have 24/7 operations. Typically, we see that for these types of operations, they will witness a significant return on investment from heat recovery – often in under a year and rarely in more than two years.
While not all recovered heat use is equal, there are still huge benefits to be had for other operations. Adoption during the winter months for example results in significant cost and carbon emissions benefits. These benefits have not been lost on some in the industry, with heat recovery applications for both space heating and water heating for human comfort, (facility heating) becoming increasingly popular in recent years.
In such cases, the heat is used as an additional heating source, which in turn reduces the requirements placed on traditional carbon-fed boilers thereby reducing separate heating fuel costs and resulting in reduced carbon emissions. In cases where the recovered heat is used for heating water, we see an efficiency of upwards of 85%, rising to 96% in fully optimised operations, and in the case of space (air) heating, an efficiency of 60 to 70% can be achieved. With such results, operations will often see a short-term return on their investment of between one to three years. So, while there are benefits regardless of the size or the industry and operational aspects of the processes, significant benefits are to be had in recovering and repurposing heat from your compressed air system. But why then is adoption so slow?
Technology application
In many small and medium-sized operations, heat recovery has simply not been a priority. Typically, and rightly so, the key priorities are usually; capacity, reliability, energy efficiency, and then heat recovery – with HRS’s playing a distant last place!
We are now witnessing a tide of change in industrial processing. Regulatory and policy pressures are driving necessary commitments towards energy efficiency. Consumers' expectations for sourcing sustainable products are extending the long arm of traceability and supply chain accountability for improved efficiency (and finally, and most importantly - the know-how and systems for heat recovery) are becoming more widespread and cost-competitive. The compressed air industry has made great advances in improving the capacity, reliability, and energy efficiency of compressed air systems addressing these priorities for operations of all sizes. And while the pace of this innovation continues unabated, ELGi is bringing cost-sensitive ‘plug and play’ Heat Recovery Systems to the market. Combined with a greater operational focus on energy auditing and system performance compliance with global standards on energy management (such as ISO50001), small and medium-sized operations can reap the benefits of heat recovery more easily than ever before.
The math is clear
The tools and technologies are available for operations of all sizes to benefit from heat recovery. A high return on investment brings immediate cost savings and more importantly, carbon emission reductions help you in lowering the company’s net carbon footprint. Heat recovery is not just the right thing to do for the future of our planet, but it makes good business sense too. Many Compressed Air Heat Recovery projects offer a relatively short payback period due to the significant energy savings achieved. Compressor Heat Recovery is a sustainable solution because it harnesses wasted energy, reduces environmental impact, and contributes to resource conservation.
Small and medium-sized companies have the tools and opportunities now to stay ahead of any regulatory changes, to meet customer (and their downstream consumer) demands for improved sustainability, and ultimately improve their never-ending productivity targets.
In addition to all this potential free energy source, there are other important aspects to consider. An example being a properly sized compressed air installation including the compressor room itself as well as it’s location to the point of use (where the compressed air is needed). The ultimate goal is therefore to recover heat from a properly sized system which is placed as close to the point of use as possible. For help with this, you can always rely on collaboration between your ESCO and your local compressed air expert, but if this article is still not as clear as the writing on your factory wall, don’t just take my word for it, the European Commission has also said: “Improved energy efficiency in industrial processes can lead to substantial primary energy savings, decarbonisation of the energy supply and subsequent reduction of CO2 emissions. The reduction in energy cost will also enable greater competitiveness.”
RELATED BLOGS
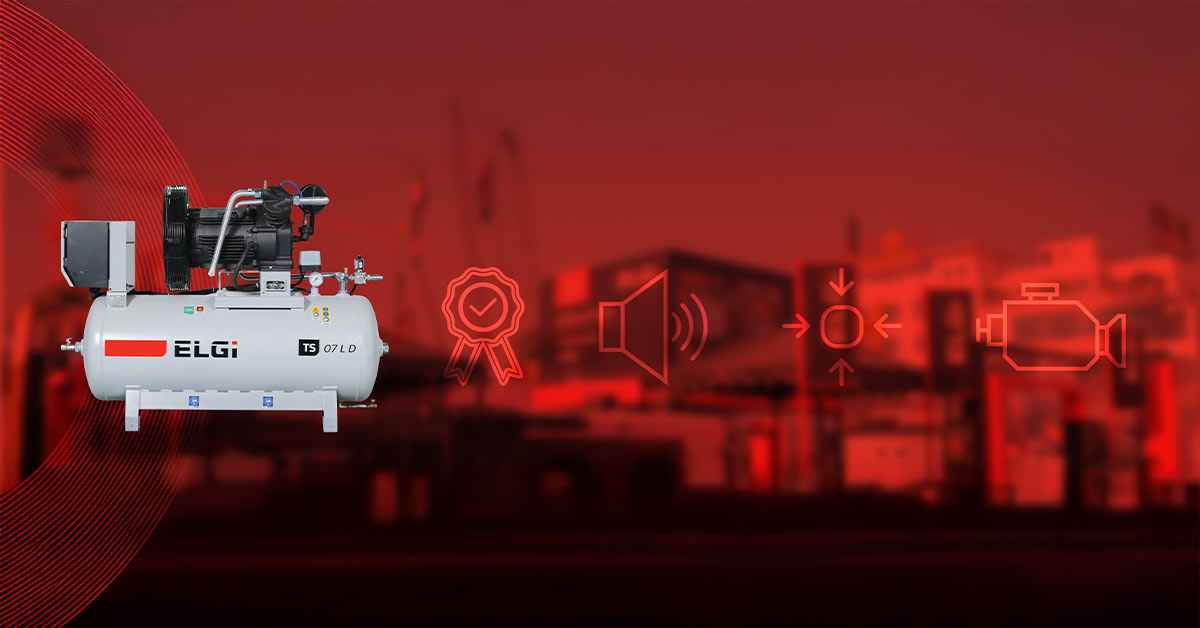
Compressed air is a critical element in many industrial operations, from powering tools to...
Read More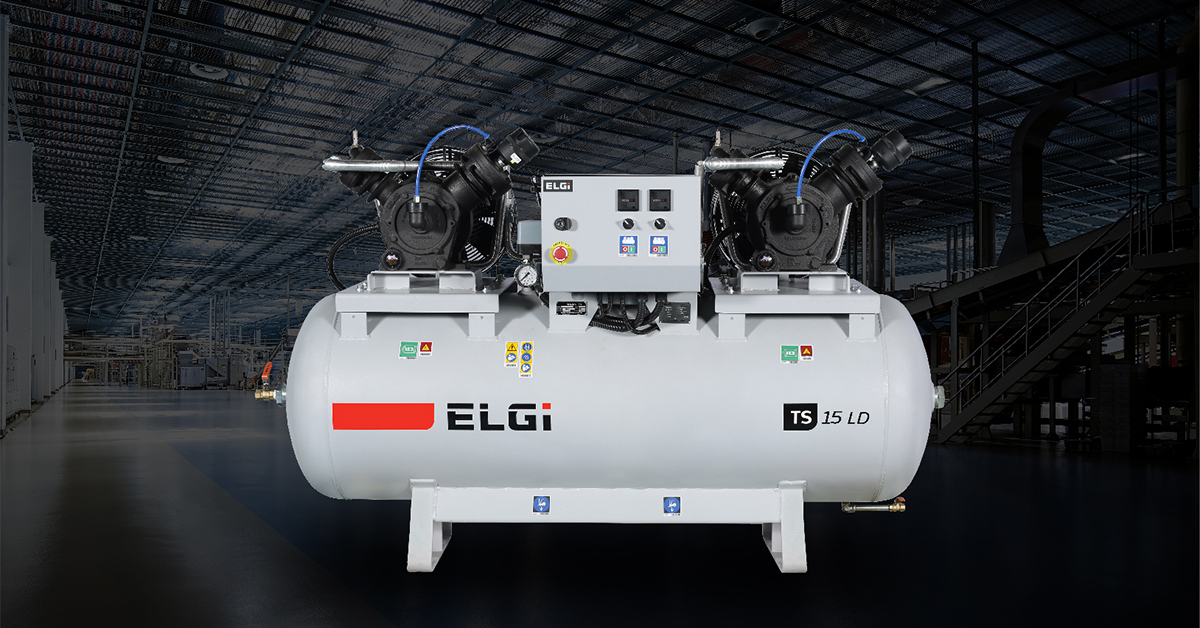
How Oil Lubricated Compressors Work and Their Role in Energy Efficiency Oil lubricated ...
Read More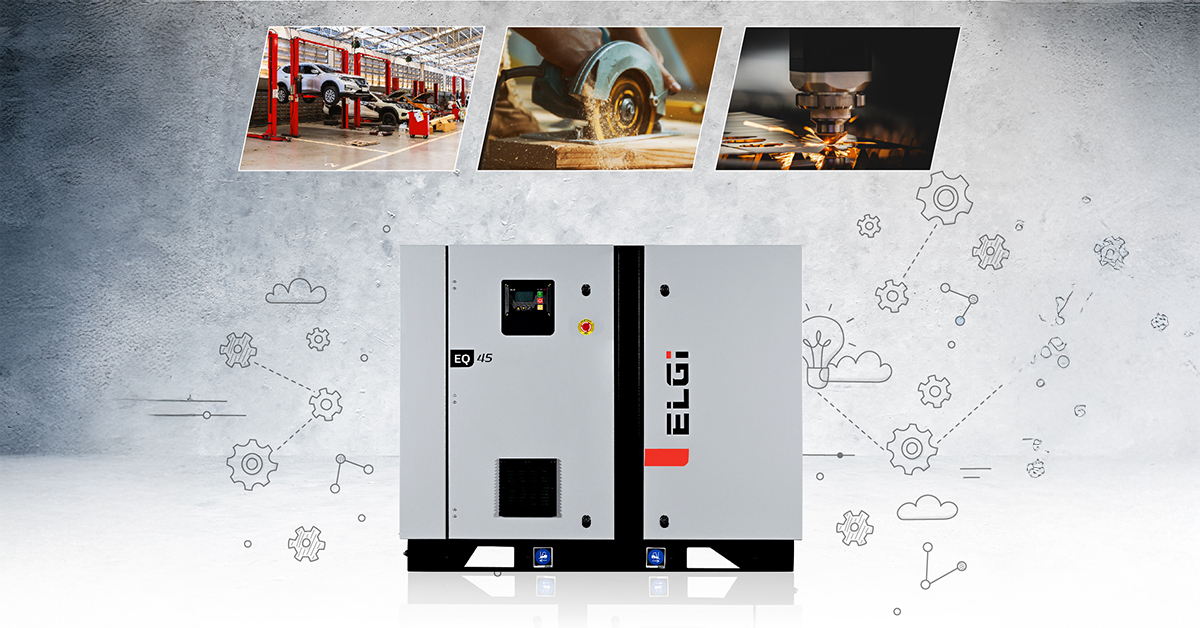
Why the ELGi EN Series is Ideal for Compact Industrial Compressed Air Solutions Busine...
Read More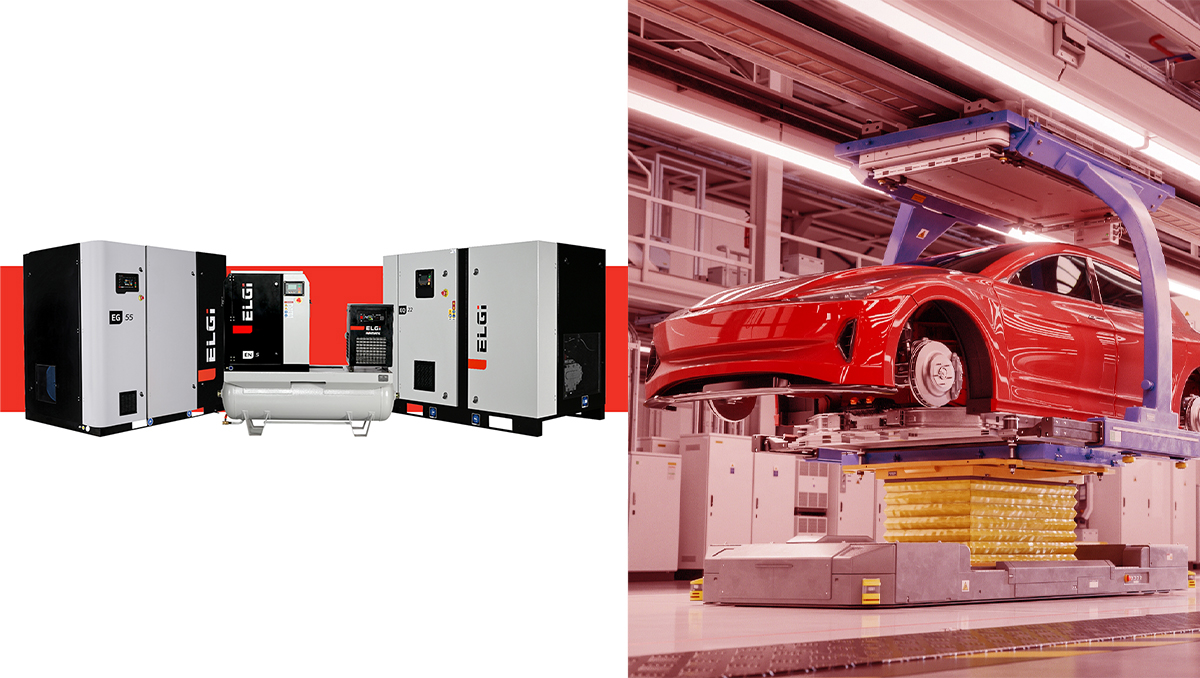
Compressed air is an invaluable resource in the automotive industry, powering everything f...
Read More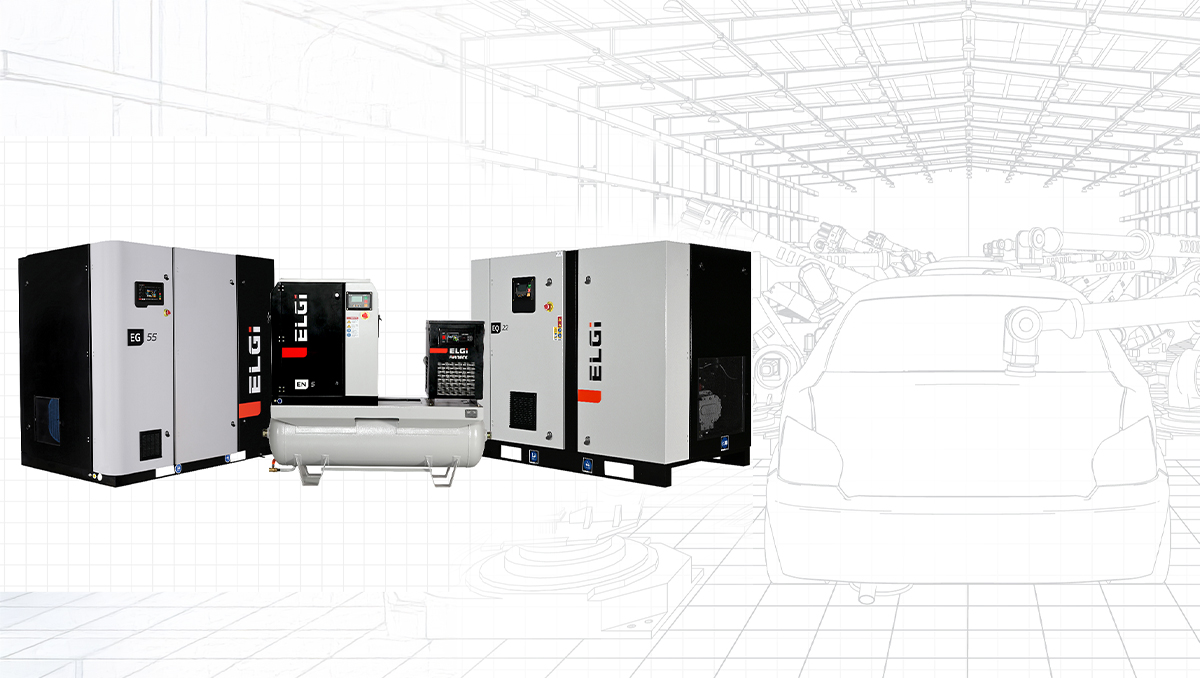
The automotive industry is one of the most dynamic and technology-driven sectors, requirin...
Read More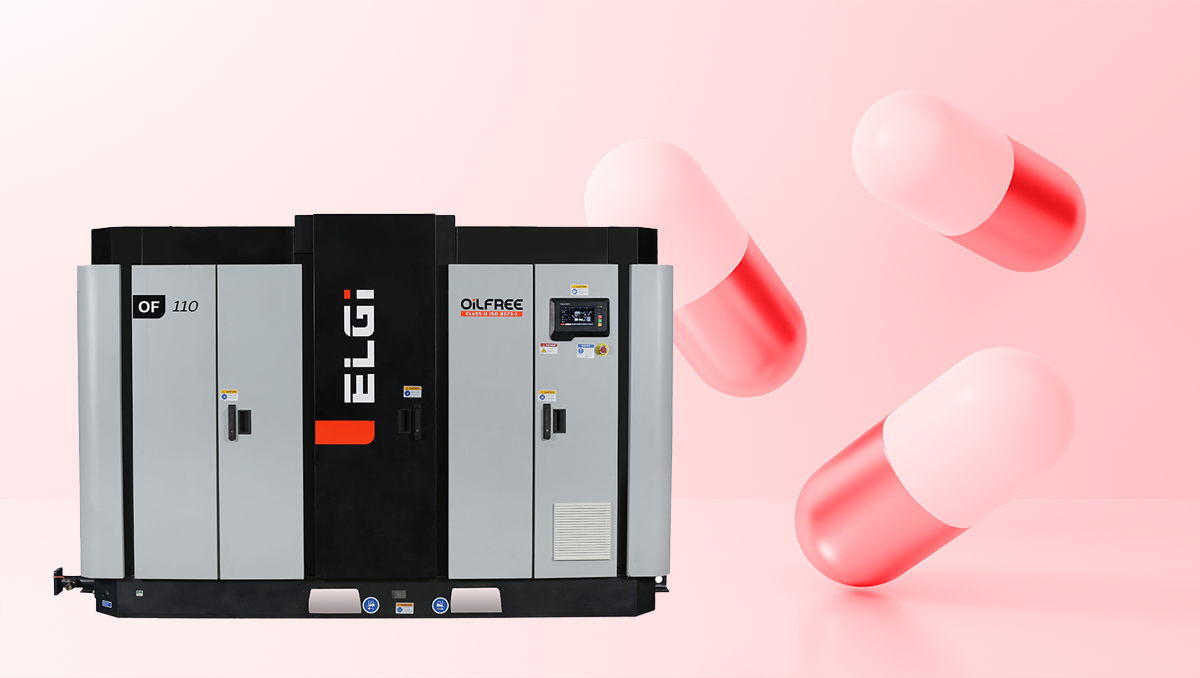
The pharmaceutical industry operates in a realm where precision, purity, and compliance ar...
Read More
Rotary screw air compressors are essential machines used in many industrial applications a...
Read More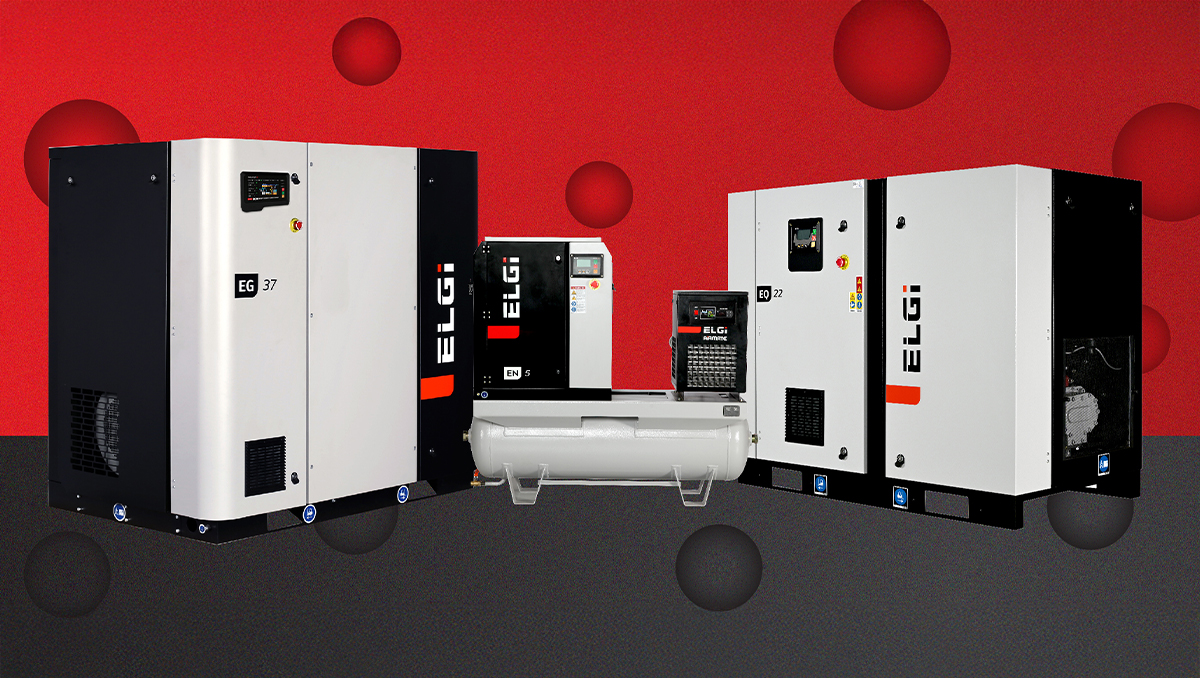
Choosing the right rotary screw compressors is crucial for your industrial operations. In...
Read More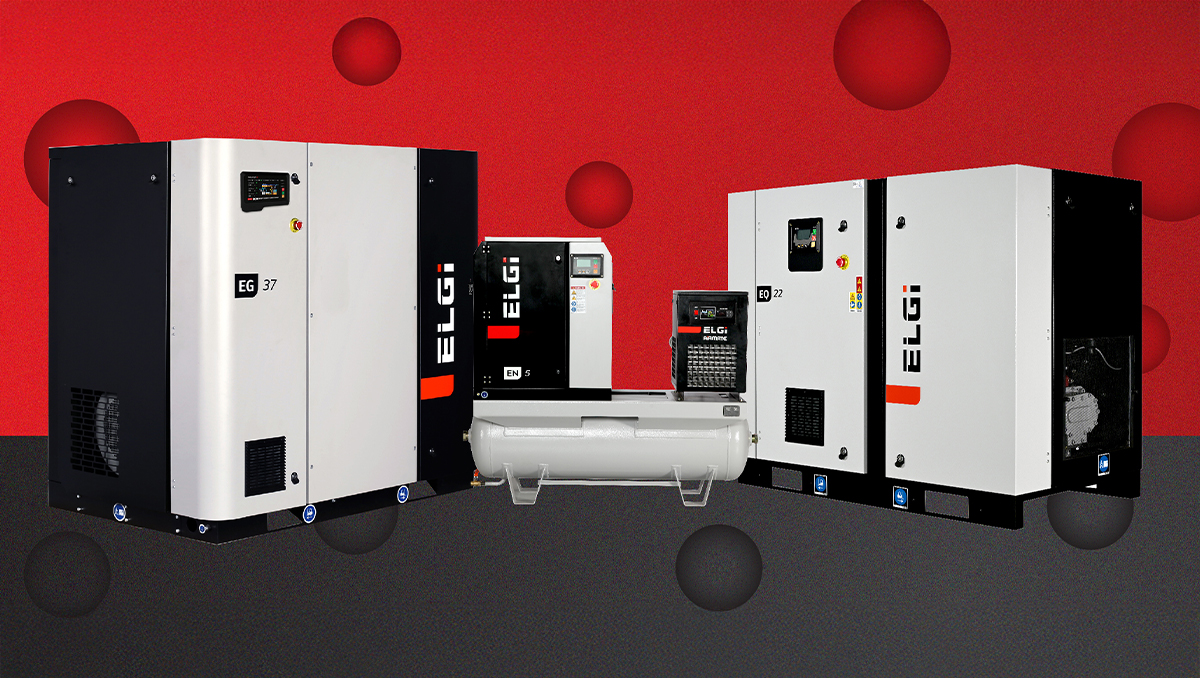
Choosing the right rotary screw compressors is crucial for your industrial operations. In...
Read More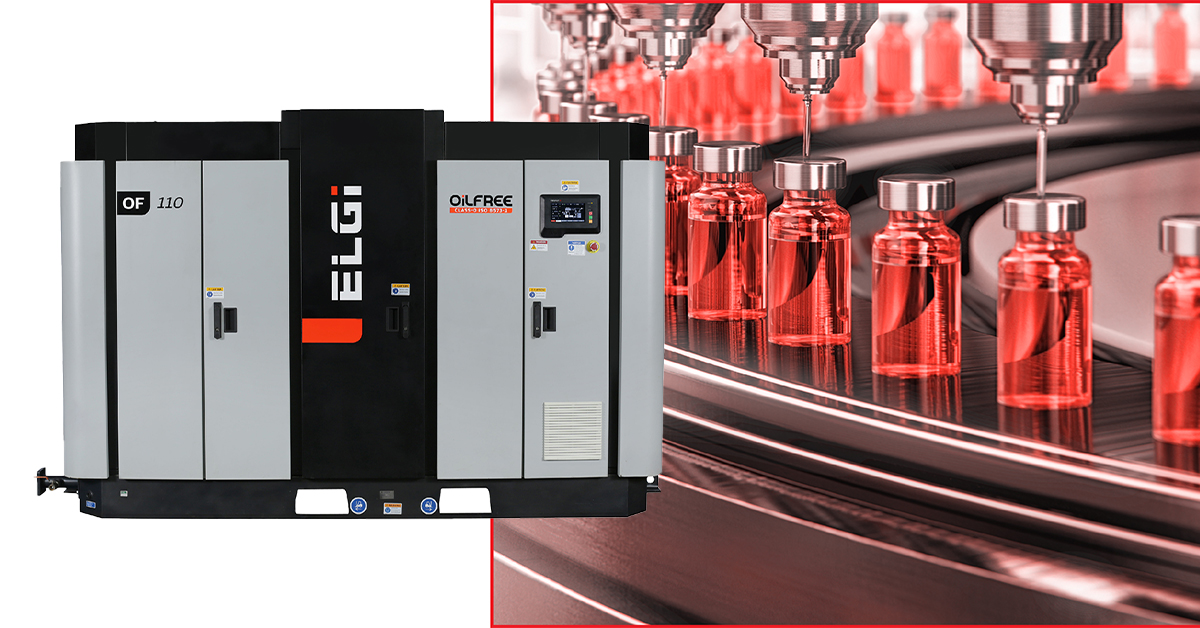
The pharmaceutical industry relies heavily on precision, sterility, and efficiency in ever...
Read MoreBe the first to get updates, learn more and join our explorative world by subscribing to our official compressed air journal.
SUBSCRIBE