The ELGi foundry was set up in 2013 to produce special castings for its air ends while addressing all the challenges of quality, cost, and delivery requirements. The ELGi foundry is Pressure Equipment Directive (PED) and ISO-9001 certified. It has an installed capacity of 9000 metric tons to make high-precision ductile and grey iron castings annually. The foundry uses a fast loop, automated no-bake chemical bonding system and employs the Furan and Amine Cold Box techniques for making ten moulds per hour.
The foundry produces castings ranging between 32 and 350 kgs, with less than 3% variation, and wall thickness between 12-70 mm. With complex internal capacities and solid shapes, over 200 variants are developed to cater to ELGi's air compressor manufacturing needs. In line with our corporate philosophy, the casting production process at the foundry aims to ensure first time right quality standards at all times.
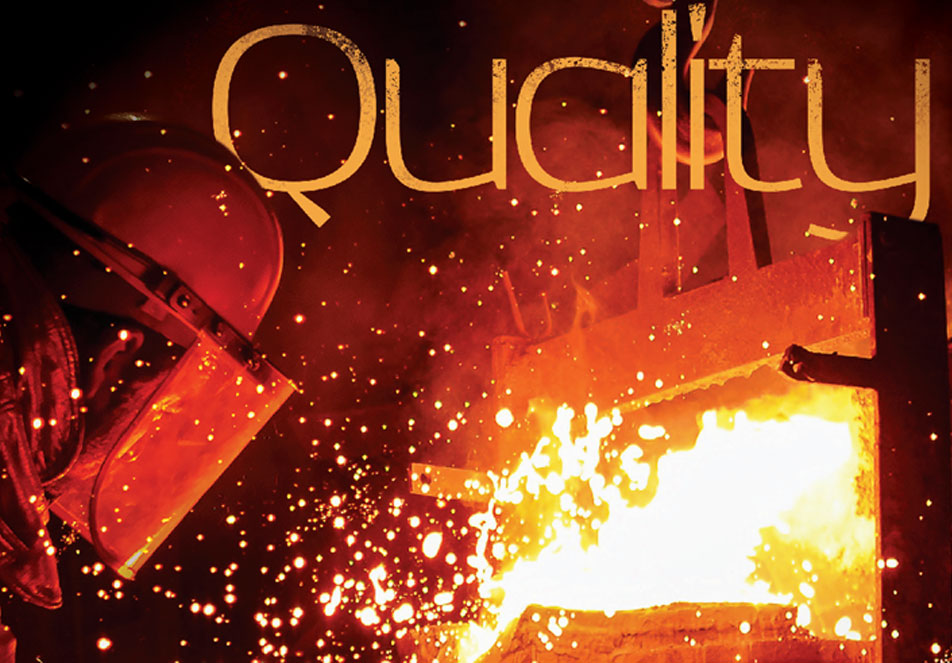
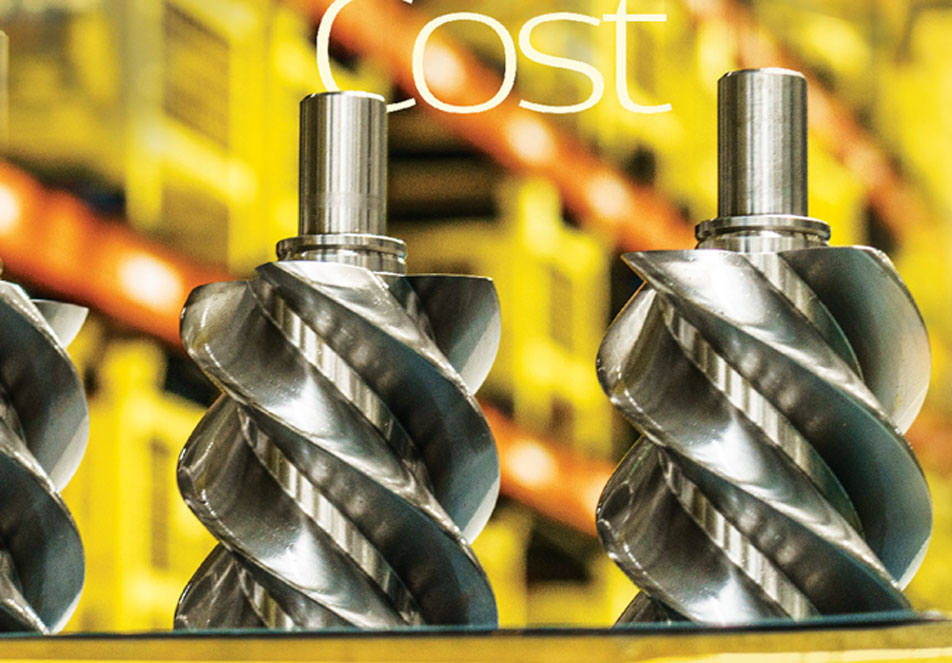
During the 1990s, customers were looking for compressors that could supply greater volumes of air; something piston compressors could not fulfill. With that began our efforts to manufacture screw compressors in-house. A tall order indeed, given that designing airends involves the development of a complex mathematical formula to define the profiles of the screw while manufacturing airends demands high precision machining with very close tolerance bands in microns. Over the past 30 years, ELGi built its knowledge of “know-how” and “know-why” of compressors to become one of the five companies in the world with the capability to design and manufacture its own airends.
In 2011-12, the Air Compressor Plant was established on over 100 acres at Kinathukadavu, near Coimbatore, India, incorporating some of the best practices in airend manufacturing globally. The state-of-the-art plant is equipped with high-precision grinding, milling, and turning machinery, with a few critical machines built by the ELGi machine-building team. The facility is also installed with mixed model conveyorised assembly lines, a vertical storage and retrieval system, a metrology laboratory, and testing equipment, ensuring high accuracy and reliability.
The pressure vessel is one of the critical components of an air compressor package. The pressure vessel division (PVD) was established in 2007 to enhance product quality and support the needs of ELGi Air Compressor packages. This integrated manufacturing setup includes designing and manufacturing air-oil separators and air receivers for ELGi air compressors. The air-oil separator vessels are used to separate the air-oil mixture in screw air compressors, whereas air receivers are used to store compressed air for direct applications.
The ELGi pressure vessel division has a manufacturing capacity of 2400 vessels per month, operating today with 100+ people and accredited with sound quality systems and processes in place. The pressure vessels manufactured are compliant with the ASME U Stamp, CE Marking as per the Simple Pressure Vessel Directive -2014\29\EU, MOM (Ministry of Manpower) for Singapore, DOSH (Department of Safety and Health) approval for Malaysia, and INMETRO certification for Brazil.
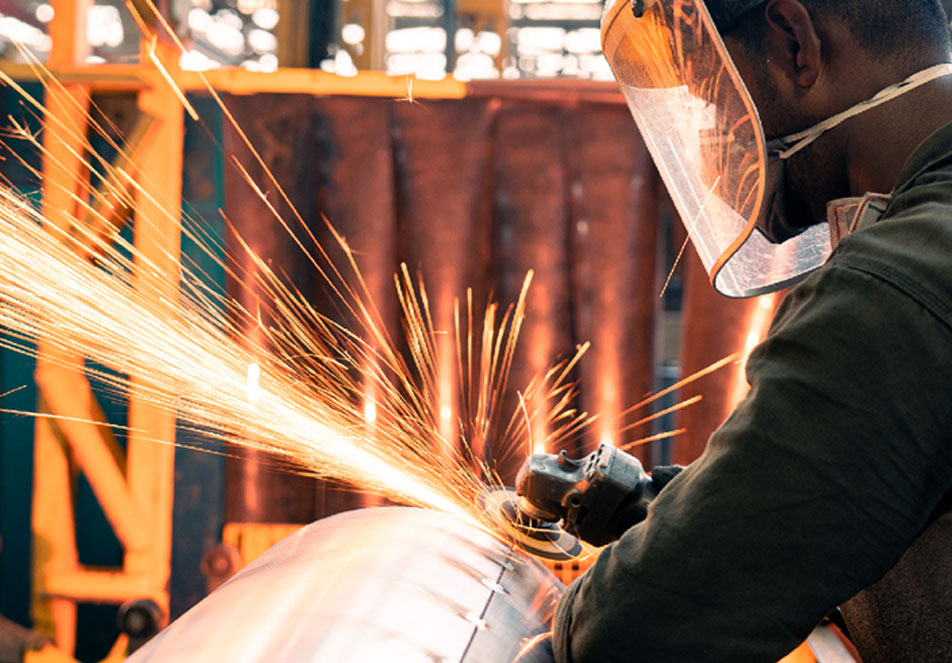
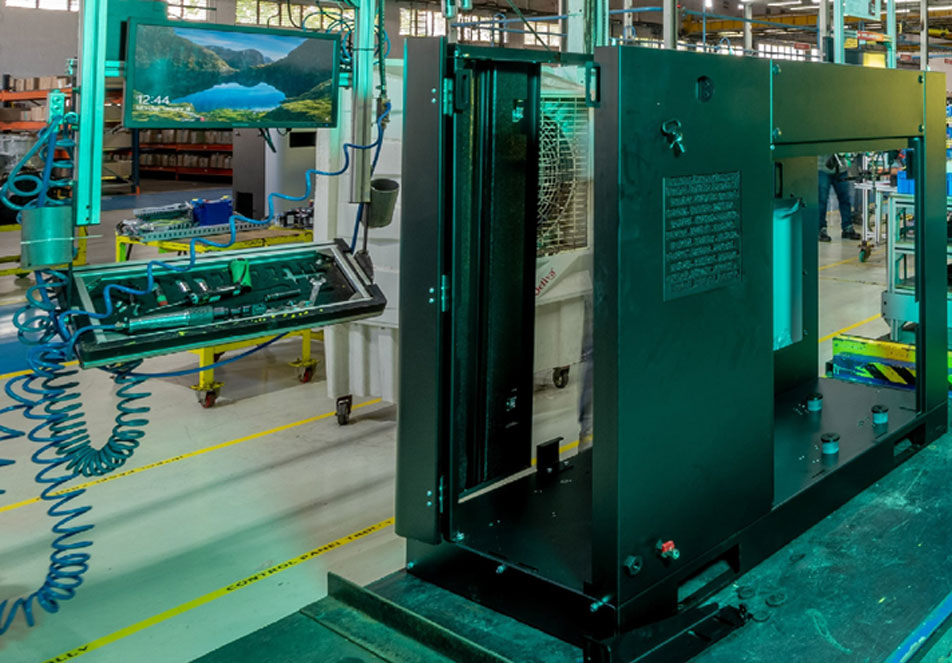
The compressor assembly is a cluster of assembly lines that integrates airends and top blocks with the prime movers (electric motors and diesel engines) and other parts and sub-assemblies manufactured in-house and components that are purchased from suppliers. The assembly process and parts are critical to the performance of an air compressor. The implementation of total quality management processes in the assembly plant has led to delivering products with zero defects and superior performance, leading to ELGi air compressors growing as the choice of customers across the globe.
The manufacturing processes and flow lines are designed to capture the quality parameters and assure adherence at every stage before passing on to the next stage. Auto-guided vehicles and digitalized feedback-based measurement systems are deployed to ensure quality in each stage. Auto data capturing systems are deployed in machine shops to track the process capabilities in real time. Every ELGi manufactured unit delivers compressed air solutions of industry-leading quality and best-in-class efficiency at competitive pricing to customers across various industrial verticals worldwide.
High-precision rotors are needed to make screw air compressors, and machines working at very close tolerances are required to produce such rotors. ELGi began custom designing and building its own rotor milling machines to meet this demand. A machine-building division was established in 2007 to develop complex in-house machines critical to the process. By effectively deploying in-house engineering talent and capability, ELGi built these machines to ensure the highest quality standards at a significantly lower cost, thereby considerably reducing production costs.
The ELGi machine tools plant produces small and big rotor milling machines (Locus). The milling machines operate with low vibration, producing tighter milled rotors. The plant also manufactures rotor deburring machines and rotor profile grinding machines. These machines, with higher rigidity, enable faster production. The machines are designed to be self-monitoring and operate with zero defects. The rotor grinding machine (Roto G) performs profile grinding and rotor finishing with very close tolerances of 15 microns. The in-house high-precision grinding and milling machines operate in ELGi’s air compressor plant.
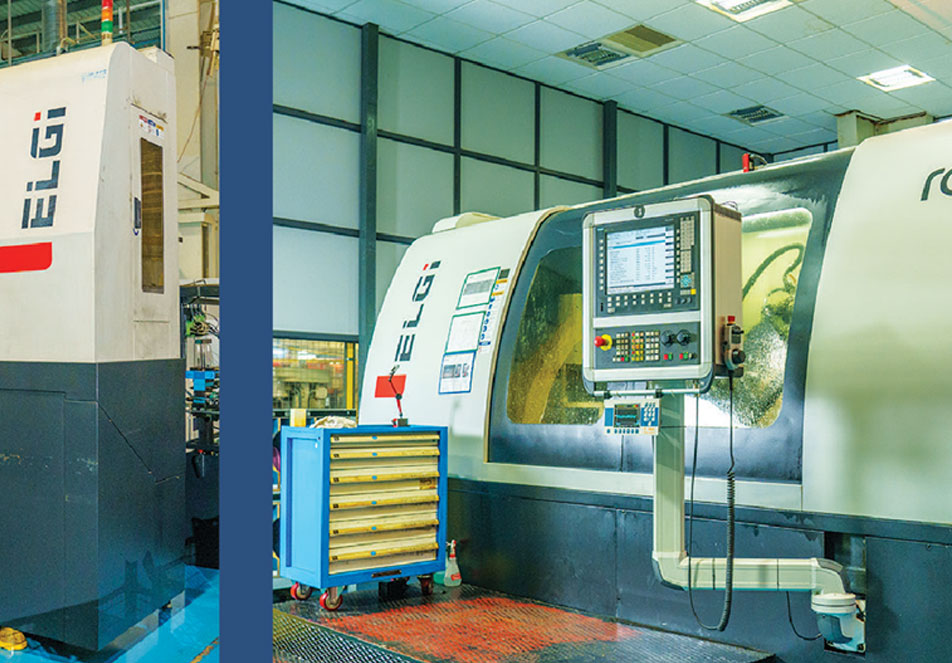
Want to be part of the dynamic ELGi growth story?
Click below to find out where you belong.