Making Screw Air Compressors Oil-free
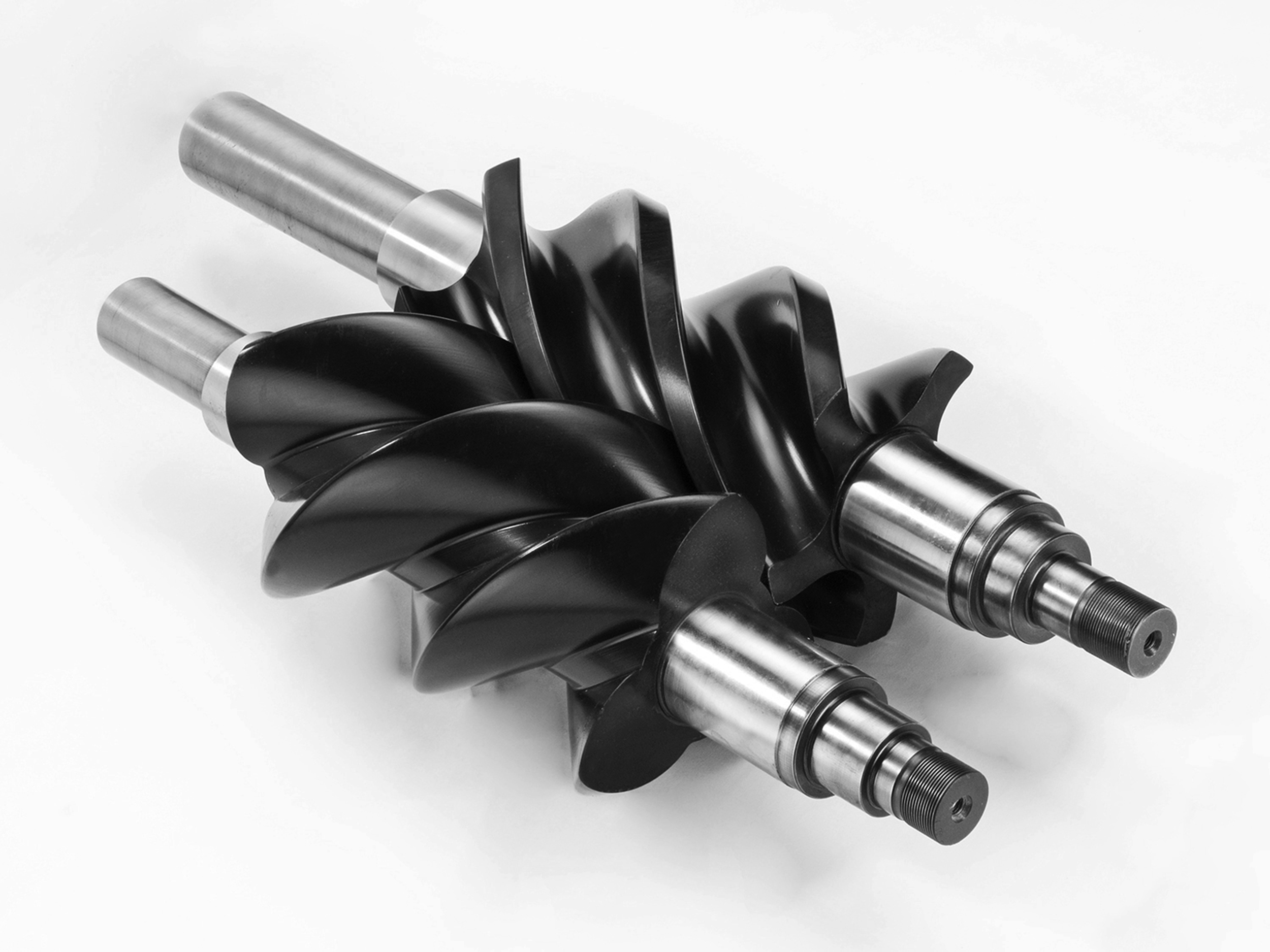
It might be hard to believe but air compressors have been around for thousands of years. The earliest known compressors were bellows, used to blow compressed air into furnaces to stoke up the heat, thereby allowing ancient men to produce stronger and better metals for tools and weapons. >
Following the invention of steam engines, they became a popular method to power air compressors. Subsequently, Internal Combustion (IC) engines began to be used as a power source for operating reciprocating air compressors. Later, as larger industries were established, they demanded more efficient compressors capable of running with minimal maintenance and for longer periods. A rotary air compressor was the answer. Both these types of compressors continued to evolve over time and today, they are both highly efficient and technologically well advanced. Conventional reciprocating air compressors though have certain innate limitations; most notable being that the oil used for lubrication is carried along with the compressed air. Filtering removes much of the oil but not all of it. For example; pre-filters, high efficiency coalescing filters and activated carbon filters remove trapped oil to a great extent.
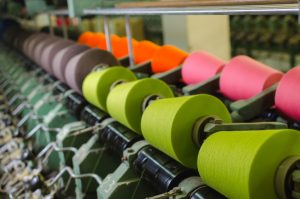
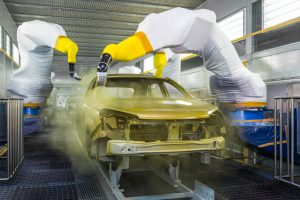
Oil-free compressed air solutions are used extensively in the pharmaceutical, textile & automotive industries.
But these filters themselves have characteristic limitations. For instance, above 20°C, coalescing filters do not remove fine oil vapours, leaving very fine particles of residual oil in the form of aerosols; and activated carbon filters are not usable at filtration temperatures above 40ºC because the carbon then absorbs the oil vapour, gets saturated, and becomes ineffective. And, filtration itself raises another problem: safe disposal of used filters to avoid environmental contamination. Notwithstanding the environmental issue however, there are several industrial applications that require compressed air that is completely oil-free. Food and beverage, pharmaceuticals, electronics, automotive painting, textiles, paper and cosmetics are typical examples. These applications demand wide operating temperatures of 0-45°C, stringent air purity standards higher than ISO 8573-Class I, high levels of safety, eco-friendly operation and some more. Even the most advanced filtration technology falls short of meeting such exceptional standards of air purity.
Plainly, lubricated compressors were not the answer. It required a radically new technology of air compression. Enter oil-free screw air compressors.
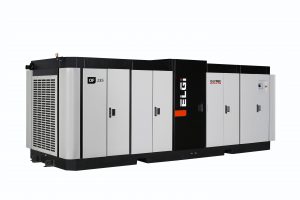
ELGi’s Screw Compressors are designed to save energy and ensure long life.
This inventive machine uses no lubricating oil in the compression chamber and hence delivers compressed air with practically no trace of oil. Additionally, because of the continuous sweeping motion of the screws – two meshing helical screws known as rotors, driven by a pair of timing gears – there is very little pulsation or surging of flow, which occurs with piston compressors. Screw compressors thus deliver smooth, pulse-free compressed air. They also tend to be compact and run smoothly with minimal vibration. Since they also employ a more efficient compression system, they not only reduce energy costs but also enable precise adaptation to end-user requirements based on careful study and analysis of their critical processes and customising with a controlled, total compressed air system, thereby also improving productivity.
Despite all its apparent advantages, oil-free screw air compressors continued to face technological and manufacturing challenges, especially pertaining to the problem of overheating due to the absence of lubricating oil in the compressor chamber. Furthermore, despite being oil-free, there was still the need for filtration as hydrocarbons and other contaminants ingested from the ambient air required to be removed prior to the point-of-use. All this began to affect their popularity to some extent. However, this also prompted a new development: oil began to be injected into the compression cavities to not only aid sealing but also provide a cooling sink for the heat of compression.
In this so-called ‘oil-flooded’ rotary screw compressor, the oil was then separated from the compressed air, cooled, filtered and recycled. The injected oil not only helped in lowering the compression temperature but also captured extraneous particulates from the incoming air, thus effectively reducing the particle loading of subsequent air filtration. Having thus overcome the initial problems that oil-free compressors faced, there was a shift from oil-free to oil-flooded compressors, which then gained popularity.
Oil-Free Two Stage: Air-Cooled Model
But the need for a completely oil-free compressor remained. This was felt keenly in industrial applications where even traces of oil in processed air could be disastrous. For instance, even minute particles of oil in precision electronic circuitry or critical semiconductor components can play havoc with electronic gadgets. Lube oil traces in processed food and beverages mean serious health risks. Pharmaceutical applications demand pristine air too. It is the same with paper mills, textiles, high-gloss painting of automobiles and many others. While Western countries had strict regulations governing the purity of air used in such critical applications, Asian countries including India and China had less stringent rules. But it was only a question of time before they too fell in line. And, although industries continued to rely on filtration to get rid of the entrapped oil, complex filtration equipment added to the cost, created air pressure drops and still did not deliver 100% oil-free air. At ELGi, this presented a situation ripe with potential.
Oil-Free Two Stage: Water-Cooled Model
ELGi embarked on developing the oil-free screw air compressor by obviating the need for oil as a medium to carry away the heat of compression. By early 2005, the first prototype was assembled and tested. And by early 2008, a test compressor was commissioned at a user’s facility for validation. Next year five more were commissioned at different locations. These models completed 10,000 hours of validation. Regular sales began by early 2011. Today, ELGi’s in-house oil-free technology with inter-cooler has been validated in demanding industrial applications for over 150,000 cumulative hours.
Inside the ELGi factory
The fully-packaged ELGi-NE series has models with high volumetric efficiency that deliver from 500 to 1800 cfm (cubic feet per minute) and pressures of up to 10 bars (kg/cm2.) Incorporating superior safety norms, these models not only have low energy losses and low air outlet temperatures but are also energy efficient and compact.
They employ two-stage compression with external water jacket inter-cooling, a unique eta-V profile rotor enabling high swept volume, low operating noise and low vibration achieved by combining radial roller bearings and 4-point axially loaded ball bearings. Innovative features like carbon impregnated SS air seals, helical grooved non-contact bronze oil seals and high-performance Visco-seals at suction and discharge rotor ends, an ingenious process of PTFE and PFA (Teflon) dry lubricant coating on carbon steel rotors, an efficient helix-angled timing gear and robustly designed cupro-nickel intercooler and after cooler, heat exchangers offering superior corrosion resistance and finally optimally designed capacity control valves; all ensure not just high efficiency but safety, durability, easy maintenance and low operating cost.
Compression is also very efficient on account of the precise clearances maintained between the helical rotors and the compression chamber, thanks to the unique eta-V profiles designed by ELGi. This rotor design reduces pressure losses and increases stage efficiencies, leading to an overall increase in adiabatic efficiency.
ELGi builds its own rotor milling machines to ensure quality rotors with lowest manufacturing cost.
Only a handful of companies in the world have this design capability. It is to be noted however, that though the machine is termed an oil-free screw compressor, it applies to only the screw chamber that forms the air compression cavity. Oil is nevertheless used in the machine – to lubricate a slew of components like the capacity control valves, air-end bearings, the timing gears and the air-end stage gear. So even though the rotors and the screw chamber do not use any lubricating oil, there is nevertheless an oil circuit comprising the oil pump, cooler, filter and oil sump. Similarly, there is also a water circuit that supplies cooling water to the intercooler, after cooler, and the 1st and 2nd stage air-ends. For ELGi, this development has been a rewarding experience. Industry watchers have it that globally, ELGi is one of only 5 corporate companies to design and manufacture oil-free air-ends.