Significance of Fixed-Speed & Variable-Speed Rotary Screw Compressors
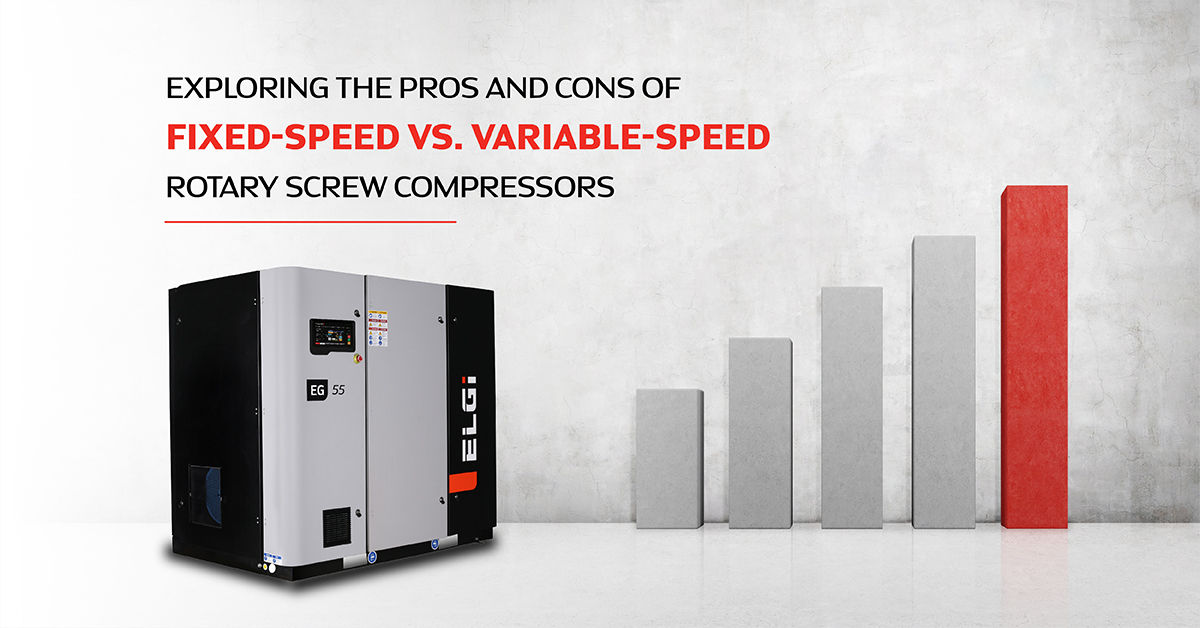
Choosing between a fixed-speed and variable-speed air compressor is crucial for any industrial enterprise. While you may have a general understanding of your facility's peak production air compressor needs, assessing the cost disparities and advantages of fixed versus variable-speed compressors is a worthwhile consideration.
In this blog, we will be exploring the pros and cons of Fixed-Speed vs. Variable-Speed Rotary Screw Compressors and delving into the factors that can influence your decision-making process.
Understanding Motor Speed Control: Fixed and Variable Speed Technologies
Two primary types of speed control govern electric motors :
fixed speed and variable speed. Fixed speed involves constant motor operation, while variable speed, facilitated by Variable Frequency Drives (VFDs), adjusts the motor speed based on load or demand. VFDs are particularly beneficial in applications prioritising energy efficiency. In both oil-lubricated and oil-free compressor models, variable frequency drives find common use in Rotary Screw Air Compressors.
Fixed speed control methods include start/stop control, load/unload control, and modulation. Each method caters to specific compressed air system requirements, offering choices based on energy efficiency and maintenance needs.
Advantages of Variable-Speed Air Compressors :
When comparing fixed-speed and variable-speed air compressors, look beyond initial costs. Consider your plant's dynamics, susceptibility to seasonal peaks, and daily shifts in air requirements. Variable-speed compressors may bring unforeseen costs if power supply issues exist. Eligible for energy savings programs, variable-speed compressors offer advantages over traditional fixed-speed counterparts, adapting to varying demands efficiently.
In contrast to fixed-speed air compressors that run at a constant speed regardless of the required output, variable-speed rotary screw compressors present a compelling alternative, offering several advantages:
Advantages of Variable-Speed Air Compressors |
Description |
1. Lower Starting Currents | Variable-speed compressors exhibit lower starting currents, reducing energy demand spikes. |
2. Energy Savings | Dynamic RPM adjustment leads to significant energy consumption reduction, often exceeding 50%. |
3. Consistent Plant Pressure | Electronic controls ensure precise pressure control, maintaining consistent plant pressure. |
4. System Longevity | Reduced stress and adaptive speed control contribute to increased compressor lifespan. |
In conclusion, opting for a variable-speed air compressor brings many advantages, from lower starting currents and substantial energy savings to consistent plant pressure and increased system longevity. These benefits, when weighed against the specific operational dynamics of your facility, can translate into significant efficiency gains and cost reductions over the compressor's lifecycle.
Examples where VSD makes sense
- Demand fluctuates significantly between jobs
- Demand varies by shift, on weekends, or seasonally
- Manufacturing processes require tight tolerances for operating pressure
Examples where fixed speed makes sense
- Demand for compressed air fluctuates a little
- The upfront cost is a significant consideration
- Using VSD and fixed-speed compressors together
Using VSD and fixed-speed compressors together
Sometimes, the most efficient compressed air solution involves combining one or more fixed-speed compressors to provide a base load with one VSD compressor that "trims" to meet changes in demand. A system with multiple smaller compressors, rather than one large compressor, also offers redundancy, enabling part of the facility to remain operational when a compressor is offline for service or repair.
Energy Incentives
A Variable Speed Drive reduces the overall load on the power grid, minimising sudden spikes in demand that could overload the grid and cause an outage. Consequently, governments and power companies may offer incentives for manufacturers to upgrade to energy-saving systems such as a VSD air compressor. These incentives can significantly offset the costs of upgrading to a new VSD air compressor and accelerate the payback period.
Fixed Speed and Variable Frequency Drive (VFD) Air Compressors
Fixed-speed air compressors and variable frequency drive (VFD) air compressors each have their respective significance and can be selected based on specific operational needs.
Criteria | Fixed Speed Air Compressors | Variable Frequency Drive (VFD) Air Compressors |
Constant Maximum Airflow | Consistent airflow, suitable for continuous fixed requirements | Airflow varies based on demand, ideal for fluctuating requirements |
Maintenance-Friendly | Generally easy-to-maintain | Complexity may lead to potential maintenance costs |
Efficiency during Low Demand | Lower efficiency during periods of low demand | Energy-efficient as it adjusts to varying demand, reducing wastage |
Suitable for Varying Airflow Demands | Not ideal for fluctuating airflow demands | Dynamically adjusts to varying demand levels, optimizing energy use |
Energy Savings | May result in energy wastage during low-demand | Significant energy cost savings due to adaptive motor speed |
Initial Investment | Lower upfront cost | Higher upfront cost, justified by long-term energy savings |
Choosing between fixed speed and variable frequency drive (VFD) air compressors depends on specific operational needs. Fixed-speed compressors ensure simplicity, reliability, and efficiency for continuous operations with stable airflow. Conversely, VFD compressors offer flexibility, energy savings, and adaptability to varying demands, making them ideal for fluctuating airflow requirements. Evaluate your unique operational needs to make an informed decision aligning with your business goals.
Variable Speed Drive vs. Fixed Speed
While fixed-speed air compressors maintain a constant speed, drawing power at the maximum demand, Variable Speed Drive (VSD) compressors, such as ELGi's EG series, operate dynamically. VSD compressors adjust speed within the minimum and maximum range, aligning air production with real-time demand. This adaptability, akin to a car's accelerator, enhances energy efficiency. Opting for a VSD compressor can lead to significant energy savings compared to fixed-speed counterparts, especially when demand fluctuates.
When picking a Rotary Screw Compressor, discerning between fixed and variable speed is vital. Fixed-speed compressors run continuously, risking energy wastage during unloaded states. On the other hand, variable-speed compressors adjust motor speed based on air demand, optimising energy use. ELGi's EG & EN series provides both options, with the VFD-equipped series ensuring automatic speed adjustments and minimising energy consumption during low demand โ an ideal choice for varying air needs.
Fixed Speed Control Methods: Start/Stop, Load/Unload, Modulation
Start/Stop Control :
Activates the compressor at pressure lows and halts at maximum set values, operating at full load or not at all.
Load/Unload Control :
Suited for medium-sized applications, this maintains compressor operation in an unloaded state, consuming around 30% of full load while not providing airflow.
Modulation :
Ideal for limited airflow variation, this method adjusts the inlet valve to modulate flow based on compressed air system pressure, allowing the compressor to operate between 50% to 100% capacity.
Use-Cases for Air Compressor Technologies
Why Does Compressor Sizing Remain Important?
Among the many air compressor technologies available, selecting the right one for your production needs is overwhelming. Proper assessment of load type is critical when choosing a Rotary Screw Compressor, considering factors such as duty cycle, operating pressure, and airflow demand. An ELGi Air Audit, conducted by compressed air experts, offers tailored insights to determine the right ELGi EN series screw air compressor for specific applications and requirements.
Why Opt for ELGi's Variable Frequency Drive Air Compressors?
Considering the significance of energy efficiency in managing operating costs, ELGi's Variable Speed Drive (VSD) air compressors, such as the ELGi EN series, emerge as a compelling choice. Regulating motor speed ensures the production of the required airflow without unnecessary energy wastage. This contributes to energy efficiency and enhances overall uptime, optimising the compressed air system
Energy consumption constitutes a substantial portion of the total lifecycle cost of an air compressor. Organisations globally seek ways to minimise operating costs, aiming for profitability while reducing environmental impact. Variable frequency drive (VFD) enabled air compressors, like the ELGi EN Series Compressor, present an opportunity for manufacturing and service companies to optimise productivity and energy consumption significantly.
How do I check the potential for energy savings through a Variable Frequency Drive (VFD)?
Every air compressor is equipped with a controller. This controller shows the running hours as well as load and unload hours. If the data shows the unload hours to be 15-20 percent of total running hours, there is a significant potential to save energy through a VFD-enabled Rotary Screw Compressor.
How do I identify the air compressor required for VFD retrofitting?
If youโre using only one air compressor to provide the airflow as per demand, the VFD can be retrofitted to the same Rotary Screw Compressor (if the saving potential has been identified). Whereas, if your facility has employed multiple air compressors to support the airflow (m3/min) demand, verify the base load and trim load requirements to choose the best possible ELGi EN series screw air compressor for retrofit. ELGi offers technical consultation to identify potential savings in your compressed air system; contact our experts.
How does one confirm the base load and trim load requirements of a rotary screw air compressor?
The best method to ascertain the base load and trim load requirements of a Rotary Screw Air Compressor is to conduct an energy audit from a qualified ELGi air expert. They will help you measure the base and trim load demand accurately.
What will happen if we install a VFD for base load requirements?
Installing a VFD for the base load alone will not offer any energy savings since the base load does not go to an unloading cycle. Hence, there will not be any savings.
For those seeking a Rotary Screw Compressor, the ELGi EN & EG series provides a range of options, including Variable Frequency Drive (VFD) models, ensuring energy-efficient solutions for diverse industrial applications.
Application-Specific Considerations with ELGi EN Series Screw Air Compressors
Various industries rely on diverse pneumatic applications, each demanding specific airflow (m3/min). Customers can explore the extensive range of ELGi EN series screw air compressors, available with or without a variable frequency drive, depending on the variability in airflow demand for their industrial requirements. In the case of a fixed-speed air compressor, it runs at a constant rate, consuming fixed power for the air demand.
Conversely, the air compressor equipped with ELGi EN Series Compressor and a variable frequency drive can dynamically adjust its speed, matching compressed air generation with demand and substantially reducing energy consumption at lower demand levels.
Choosing Between Fixed and Variable Speed Rotary Screw Compressors
When selecting the optimal Rotary Screw Compressor for automotive air tools, a crucial decision point emerges โ choosing between a fixed and variable speed system. A fixed Rotary Screw Compressor operates at a constant speed, proving efficient when running at 100 percent full load. However, it becomes inefficient when the motor unloads, wasting energy.
On the other hand, a Variable Speed Rotary Screw Compressor adjusts its motor speed based on the quantity of needed air, dynamically producing only the required amount of air and utilising the necessary energy, thereby minimising waste. Adopting variable-speed compressors can result in an average energy consumption reduction of up to 35 percent.
Why should you opt for ELGi's variable frequency drive air compressors?
Here are a few reasons to consider ELGi air compressors with variable frequency drives for your applications:
Energy efficiency
In ELGi air compressors with variable frequency drive, the speed of the motor is regulated, ensuring the required airflow is produced and no energy is wasted. The VFD air compressor greatly benefits industries and applications with varying airflow (m3/min) demands.
High Uptime
The regulated compressed air supply helps optimise the compressed air system and reduces the chances of equipment wear, thus offering higher uptime.
Energy constitutes a substantial 75% of an air compressor's total lifecycle cost, a crucial factor in operational expenses. Global organisations seek ways to minimise costs, enhance profitability, and reduce environmental impact. Variable Frequency Drive (VFD) compressors present an opportunity for manufacturing and service companies to optimise productivity and energy consumption, offering energy-efficient solutions for heightened profitability.
ELGi offers its customers a wide range of compressed air solutions, from fixed speed to variable frequency drive-enabled rotary screw air compressors depending on the end-use application demands
Our compressed air experts can help you select the right air compressor for your application. Contact us at enquiry@elgi.com
Here are some points to consider when choosing a suitable air compressor for your business.
Airflow requirements
Airflow, the volume of air produced by a compressor at a specific pressure over time, is key in pneumatic applications. To ensure seamless production, assess task frequency and simultaneous job count before compressor selection. An underpowered compressor risks insufficient flow and pressure, potentially disrupting production. Prioritise an accurately sized air compressor to meet pneumatic application demands, fostering a smooth and trouble-free production line.
Pressure requirements
Pressure (bar g) is the force exerted over a surface with a certain area. It is ideal to select the compressor based on the working pressure needed to operate pneumatic applications. If an air compressor is operated at a higher pressure than required, it will consume significantly more energy to achieve that additional pressure rating
Duty Cycle
The duty cycle refers to the operation cycle or the time the compressor runs to provide compressed air at a consistent pressure and specific flow rate. This is one of the critical parameters that help decide if a fixed speed drive or a variable frequency drive (VFD) is required.
Additionally, we recommend conducting an ELGi Air Audit with one of our compressed air experts to determine the right air compressor for your application and requirements.