Examining Innovation, Sustainability, and Customer Focus in Air Compressor Manufacturing
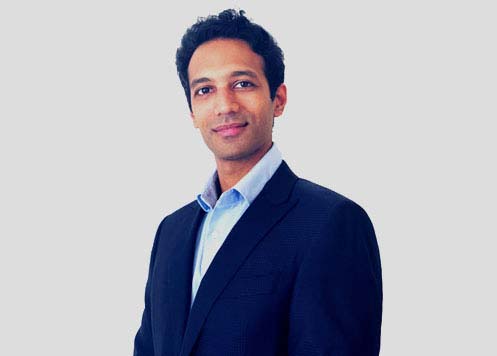
In an exclusive interview with Industry Outlook magazine, Anvar Jay Varadaraj, Chief Operating Officer of ELGi Equipments Limited shares his views on the current challenges with regard to air compressor technologies and the avenues that can be innovated. He also provides pointers for customers who are looking to integrate air compressor facilities in their factories. He is part of the fourth generation of ELGi's promoter group. He started with ELGi in 2015, where he established ELGi's marketing and communications function and activities to build the brand and support the company's "CK2" aspiration.
From your perspective, what are the primary challenges faced by air compressor manufacturers in terms of innovation and meeting customer demands?
There are three dimensions to be considered when it comes to innovation in air compressors. One is the energy efficiency, two is the quality of air utilized and the third factor is the ability to support downstream applications.
The current air compressor technology is close to engineering limits with regard to efficiency. So, customizing based on the customer’s needs takes priority. This becomes even more apparent in energy-intensive operations like textiles and pharmaceuticals, where every ounce of efficiency must be leveraged. When it comes to the quality of air, customers demand a higher quality of air. Currently, an oil-lubricated screw air compressor will discharge oil at the end of the application, so when we try to reduce that, the traditional approach is to reduce tolerance within the compressor so that it utilizes less oil; therefore, less oil will be discharged.
With regards to downstream filtration, we need to look into carbon filtration, separators etc. But these are minor increments with regards to improving the quality of air. The dramatic improvements would be to make an air compressor to not use oil at all. But the trade-off with oil free compressors is they lose efficiency and reliability. This would lead to higher up-front costs.
Finally, making accessories an affordable part of the consumer set. For example, variable frequency drives help to streamline power consumption. No factory will be operational 100% of the time. It will operate for a few hours and remain idle for a specific duration, but the compressed air will consume energy to remain compressed, and it will consume energy when no work is being done. That is unloaded power. Variable frequency drives smooth power consumption when there is a variable pattern in power usage. The goal is to have a good R&D track that helps make VFDs more affordable to the point that there would be no difference between a compressor with one and without one.
What advice would you like to give to customers to maximize the full capability of their air compressors?
They have to select a suitable air compressor. This is where the majority of the battle with regard to efficiency and reliability is won. Customers should be thoughtful about matching the size of the requirements in terms of flow and pressure to the suitable air compressor. If you have a particular flow precondition at a specific pressure, urge the vendor to give them the corresponding compressor that best matches their requirement. A common mistake customers make is buying over-the-requirement compressors based on insecurity under the assumption that they may be of use in the future.
INDUSTRY OUTLOOK